Alles uit de kan met GC/MS voor het bepalen van de gasreinheid van subassemblies voor de halfgeleiderindustrie
De spectaculaire groei van de Nederlandse halfgeleiderindustrie heeft Pneutec, een competence center van Aalberts advanced mechatronics in Hoofddorp, geen windeieren gelegd. Inmiddels meer dan 100 medewerkers assembleren in cleanrooms fluid control systemen voor de high-tech OEM-markt. Het is essentieel dat kunststoffen in deze systemen geen of zo min mogelijk chemische stoffen afgeven. Assemblages worden op reinheid gekwalificeerd door middel van een specifieke test, het zogenaamde total organic carbon (TOC). Development engineer Eli Vanquaille en operators Richard Bos en Peter Wijsman gebruiken de GC/MS met thermisch desorptiesysteem niet alleen voor deze ‘bread & butter’ tests, maar ook voor onderzoek naar nieuwe materialen.

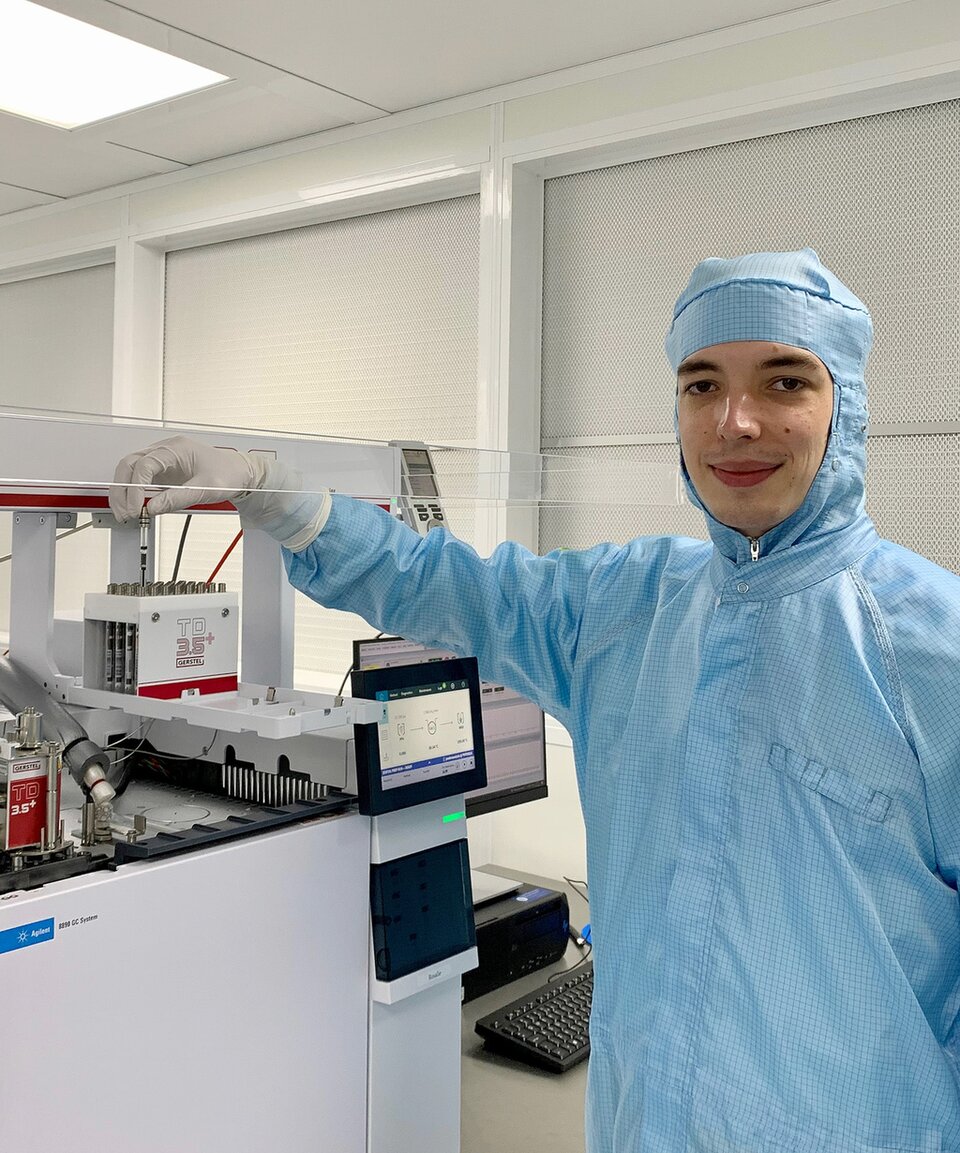
Development engineer Eli Vanquaille: “Door het intern uitvoeren van de GC/MS-bepaling op gasreinheid kunnen we sneller leveren, sneller eventuele productieproblemen oplossen en meer doen aan onderzoek en ontwikkeling.”
In de innovatiewedloop om steeds meer transistoren op een chip te krijgen is de in lithografiemachines toegepaste lasertechnologie een van de belangrijkste factoren waarmee je het verschil kan maken. Met de nieuwe EUV-technologie als meest recent hoogstandje slaagt men erin om met steeds kleinere golflengtes de meest minuscule patronen op een chip te maken. Voor optimale werking van die lasers wordt er alles aan gedaan om verstoringen te voorkomen, zoals het vermijden van trillingen.
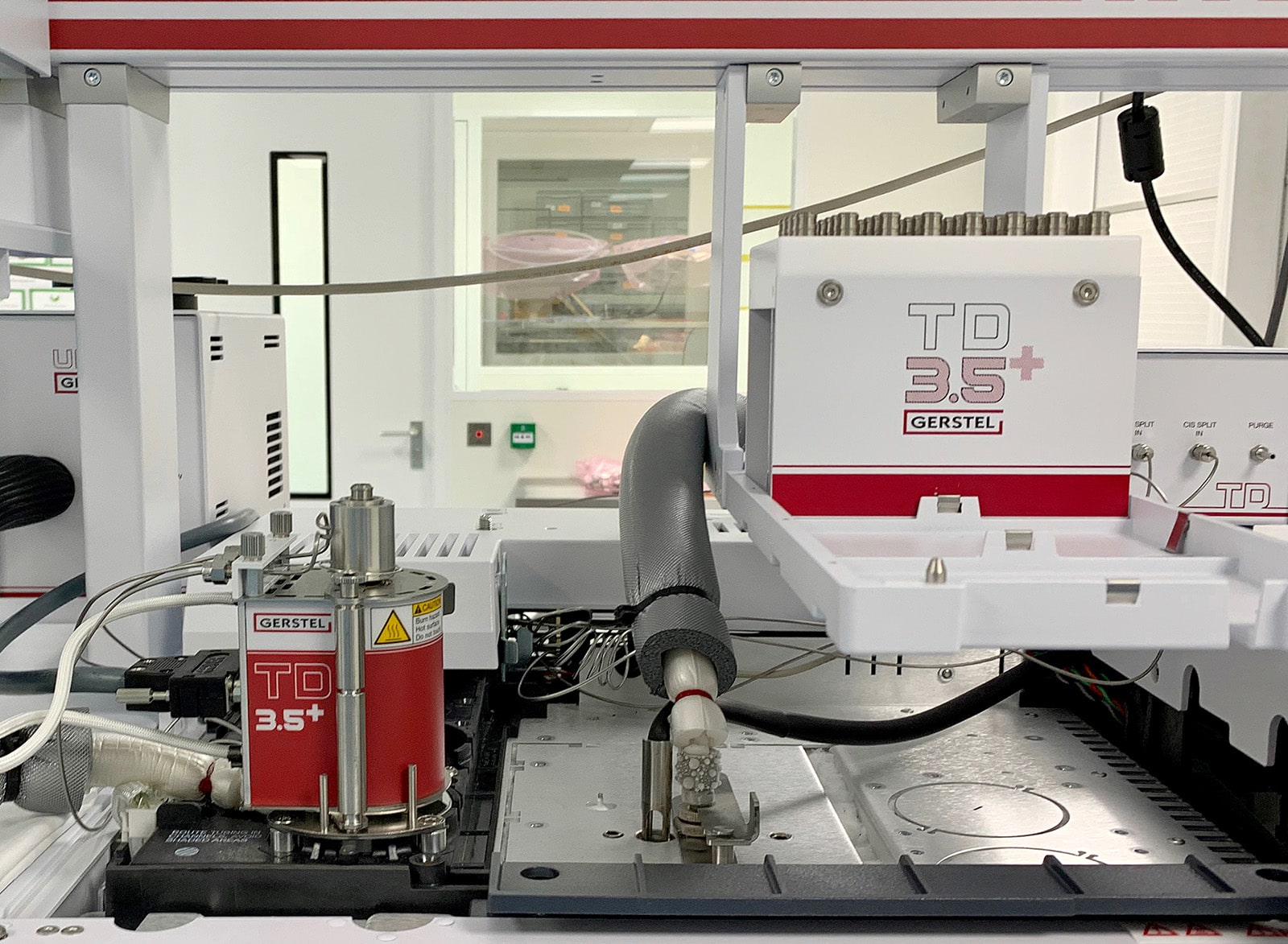
De TDU maakt het mogelijk om de geadsorbeerde moleculen uit het koolstof buisje te desorberen en gereed te maken voor GC-injectie.
Om binnen de nanometer-specificaties te blijven is het ook zaak dat de lichtgolf zich kan verplaatsen door een vacuüm met zo weinig mogelijk verstorende stofdeeltjes en/of gassen. “De machines doen hun werk in een cleanroom met gespecificeerde maximale contaminatieconcentraties. De laser zelf bevindt zich in een ultrahoogvacuümkamer, waarin nog minder vervuiling aanwezig mag zijn. Met de steeds grotere nauwkeurigheid van de machines groeit de noodzaak om daar nog beter grip op te krijgen. Stofdeeltjes en gassen kunnen er immers voor zorgen dat het licht op een net iets andere manier wordt gebroken dan gewenst. Met een verschuiving van de brekingsindex –hoe klein die ook mag zijn– zit je dan al snel net naast het punt waarop je het licht had willen projecteren. Op nanometerniveau zit je dan –overdrachtelijk gezien– met de auto in de berm!”, aldus Eli Vanquaille, development engineer bij Pneutec, een competence center van Aalberts advanced mechatronics.
Schone leidingen
De OEM-leveranciers aan wie Pneutec levert, beschrijven minutieus voor elk onderdeel de specificaties. Deze zijn in veel gevallen een afgeleide van de overall eisen aan het systeem. Zo mag er bijvoorbeeld een bepaalde hoeveelheid aan deeltjes en organische verbindingen vrijkomen in de hoogvacuümkamer. Er leiden echter meerdere slangen en leidingen naar die kamer, wat betekent dat er per subassembly of slangenbundel een aparte specificatie wordt afgegeven, waarbij de som der delen onder de overall specificatie voor de hoog-vacuümkamer blijft.
Voor Pneutec betekent dit dat voor iedere subassembly –een samenstel van leidingen– naast het testen op de aanwezigheid van deeltjes (APT; ‘airborne particulate testing’) de gasreinheid moet worden vastgesteld; hoe schoon die is op moleculair niveau. Bij deze ‘total organic carbon’ (TOC) bepaling gaat het met name om koolwaterstoffen met drie tot twaalf C-atomen, dus van vluchtige verbindingen met een kookpunt van 40 °C tot zwaardere met kookpunten tot 200 °C. Deze worden naar het hoogvacuümgedeelte meegevoerd door het medium, dat door de subassembly stroomt. Het uitgassen van organische componenten uit het plastic van de leidingen, met name thermoplasten als PU en PFA, levert hieraan een forse bijdrage. Ook lijmen, die bij de koppelingen in de subassembly zijn gebruikt, kunnen voor ongewenste contaminatie met organische stoffen zorgen. De buitenkant van de subassembly kan ook bijdragen aan organische contaminatie, maar die komt niet in het meest kritische gedeelte van de machine. Enkel het medium dat door de subassembly stroomt, bereikt het hoog-vacuümgedeelte.
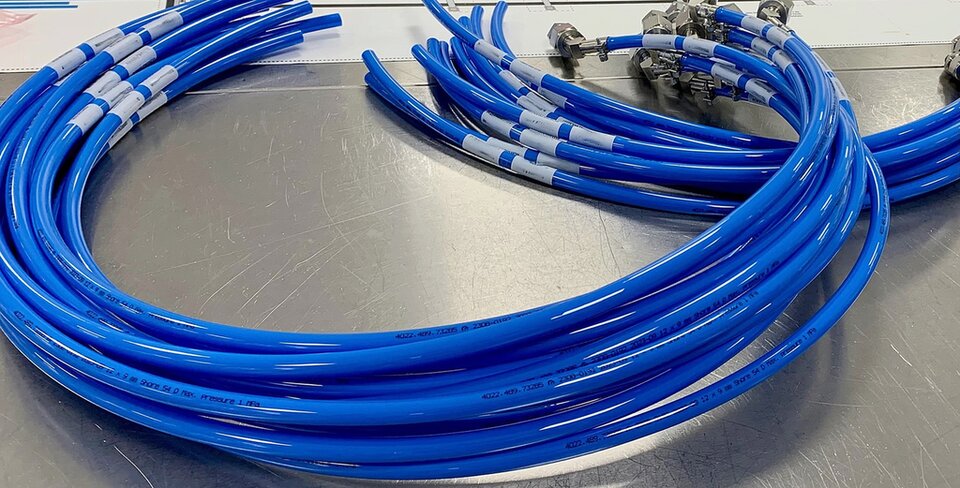
Kunststof slangen zoals deze worden in assemblages toegepast.
Testen in eigen huis
Vanaf de start van de productie van high-tech assemblages is het testen op gasreinheid uitbesteed bij een service provider. Verschillende ontwikkelingen maakten dat dit niet langer de beste optie was en ruim een jaar geleden is besloten om het testen zelf te gaan uitvoeren. “We hebben in de loop der tijd de productiecapaciteit flink moeten opschroeven, waarbij onze klanten ook nog eens om kortere doorlooptijden vroegen. Dat vergde meer testcapaciteit bij de serviceprovider. Alleen kreeg die het zelf ook steeds drukker, wat resulteerde in oplopende leadtimes. Door dit gespecialiseerde testwerk intern uit te voeren konden we een flinke efficiencyslag maken, omdat we nagenoeg niet meer te maken hebben met transport- en wachttijden. Bovendien kunnen we veel beter inspelen op onvolkomenheden in het proces. Als er eens iets fout gaat, kan je snel en precies achterhalen waar het probleem zit en het ook sneller verhelpen. Last but not least houd je nu ook kennis binnen de deur, die je kan inzetten voor onderzoek en ontwikkeling”, vertelt Eli.
Pneutec en Aalberts
Pneutec in Hoofddorp is opgericht in 1987. Het bedrijf begon als handelsorganisatie van onderdelen in pneumatische oplossingen. Al snel bleek dat klanten het waardeerden als reeds in een vroeg stadium –de engineeringfase– wordt meegedacht over de beste oplossing. Hiervoor voorziet het bedrijf in kennis van pneumatiek, vacuümtechniek, dempingstechniek en fluid control. Vanuit het zoeken naar totaaloplossingen op het gebied van de beheersing van stromingen en bewegingen was het een logische stap om zelf onderdelen te gaan samenstellen. Dit resulteerde in de inrichting van een schone productieruimte met speciale machines en instrumenten, alsook de groei tot gespecialiseerde leverancier van systemen en machines voor Original Equipment Manufacturers (OEM).
Sinds 2017 maakt Pneutec deel uit van Aalberts advanced mechatronics en wordt er meer ingezet op de semiconmarkt. Hiervoor zijn de cleanroomfaciliteiten sterk uitgebreid en gebeurt sinds een jaar ook het testen van de speciale assemblages in-house, in een aparte testruimte.
Wiel al uitgevonden
Eli stond als projectleider voor de uitdaging om bij een productiebedrijf een best wel ingewikkelde analytische infrastructuur op te zetten. “We hadden hierbij echter het geluk dat ons zusterbedrijf Lamers High Tech Systems in Nijmegen al meer dan tien jaar eenzelfde soort metingen uitvoert. We hoefden dus geen nieuwe analysemethode te ontwikkelen. Bovendien was het niet nodig om het hele proces van het zoeken en selecteren van een leverancier te doorlopen, omdat Lamers meerdere systemen in gebruik heeft die zijn geleverd door Da Vinci Laboratory Solutions, en daar meer dan prima ervaringen mee heeft. Kortom: alles wat specifiek is aan het gebruik van het systeem voor onze toepassing hebben we binnenshuis geleerd, en voor alles wat met de bediening, troubleshooting en onderhoud van het systeem te maken heeft, kunnen we bij Da Vinci terecht. Voor dat laatste hebben we een driedaagse training op locatie gehad van Da Vinci. Heel nuttig door de focus op de praktijk. Als dit gebeurt, dan zit dat erachter en kan je het zo oplossen. Zo moet je de bron demonteren en schoonmaken, enzovoorts.”
GC/MS
In principe volstaat GC met FID om aan te tonen dat het product aan de specificaties voldoet. “Uit het piekje in een chromatogram kan je met deze detectietechniek alleen afleiden dat het om een koolwaterstofverbinding gaat, maar niet om welke. Door te kiezen voor GC/MS kunnen we kwalificeren èn kwantificeren. Dat geeft ons extra analytisch inzicht bij het oplossen van afwijkingen in de productie. Ook kunnen we met GC/MS veel meer data genereren voor onderzoek naar bijvoorbeeld nieuwe materialen”, aldus Eli.
Studie naast je werk
Eli Vanquaille had in de zomer van 2020 als bachelor-student werktuigbouwkunde aan de TU Delft een bijbaantje voor het tekenen van werkinstructies bij Pneutec. “Ik had er wel oren naar om er langer te blijven werken, want alleen studeren vond ik te weinig uitdagend. Geleidelijk werd ik voor andere projecten ingeschakeld; ruim een jaar geleden voor het opzetten van de faciliteiten voor de bepaling van gasreinheid. Inmiddels ben ik met mijn master materials science & engineering begonnen, een richting die is ingegeven door het werk dat ik hier doe. Daar doe ik wel wat langer over, want waar ik ooit begonnen ben met twee tot drie dagen per week bij Pneutec, werk ik er nu soms wel vijf. Studeren doe ik in de weekenden en ik neem twee tot drie weken vrij om me voor te bereiden op tentamens. Dat werkt prima voor mij!”
Door te kiezen voor GC/MS kunnen we kwalificeren èn kwantificeren. Dat geeft ons extra analytisch inzicht bij het oplossen van afwijkingen in de productie.
Parts per billion
De GC/MS meet in het parts-per-billion (ppb) bereik, maar de feitelijke concentraties liggen nog veel lager. Daarom is het zaak om voldoende stofhoeveelheid in je analysemonster te concentreren. De sampling vindt plaats op een adsorptiebuisje, waarna via thermische desorptie de moleculen geconcentreerd op de GC-kolom worden gebracht.
Eli legt uit hoe dat in zijn werk gaat: “We monteren ons product, veelal een stuk slang met een koppeling aan beide kanten, in een testopstelling en sturen daar vanaf de ene kant ‘extreme clean dry air’ (XCDA) doorheen. Deze extreem schone perslucht, die is gedroogd, gefilterd en gezuiverd, neemt de moleculen mee die van het materiaal afkomen. Aan de andere kant vangt een adsorptiebuisje met actief kool alles op wat vrijkomt uit het product. Van ieder product wordt een van te voren bepaald volume gesampled en het hele proces neemt ongeveer anderhalf uur in beslag.
Na het samplen wordt het buisje in een thermische desorptie-unit (TDU) geplaatst. Deze verwarmt het buisje op tot 300 °C en stuurt er helium doorheen in de omgekeerde richting als bij het samplen. Op die manier komt alles wat aan het koolstof was gebonden, weer los. In een met vloeibaar stikstof gekoeld gedeelte worden vervolgens de moleculen ‘getrapped’. De injectie-inlet wordt vervolgens snel opgewarmd, zodat het monster in een nauwe band door de GC-kolom gaat en de scheiding van individuele componenten scherpe pieken oplevert, die in de massaspectrometer verder kunnen worden gekarakteriseerd.
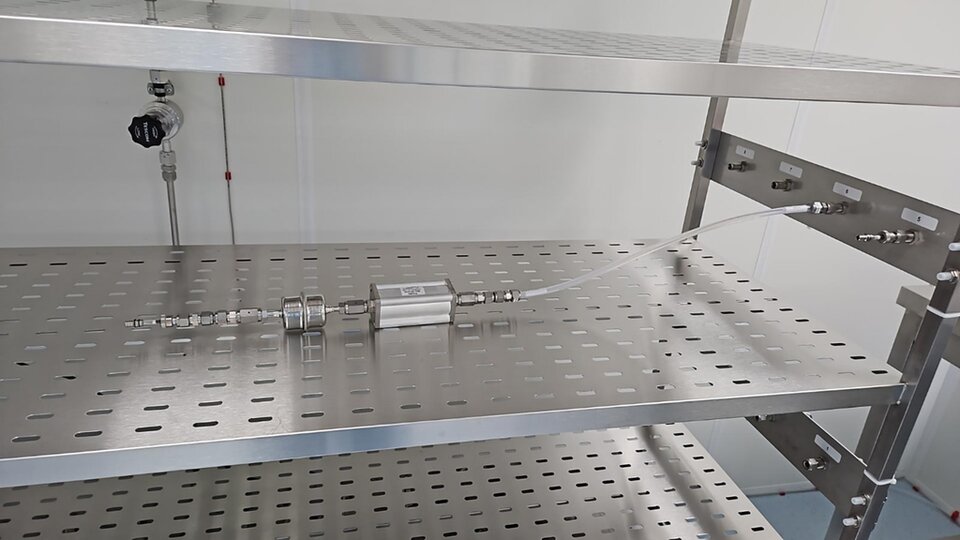
Extreem schone perslucht wordt van één kant door het te testen object gestuurd. Aan de andere kant vangt een adsorptiebuisje met actief kool alles op wat vrijkomt uit het product.
Door te kiezen voor GC/MS kunnen we kwalificeren èn kwantificeren. Dat geeft ons extra analytisch inzicht bij het oplossen van afwijkingen in de productie.
Op rolletjes
De kwalificatiemethode is inmiddels zodanig dichtgetimmerd, dat die grotendeels geautomatiseerd kan worden uitgevoerd. Zo pakt de MPS robotic sampler van GERSTEL de adsorptiebuisjes op, plaatst ze in de thermische desorptie-unit en haalt ze er ook weer uit. Ook de rapportage van de meetresultaten vindt geautomatiseerd plaats. Dat is grotendeels de verdienste van Richard Bos, een van de operators. Met behulp van door hem geschreven programma’s kan je met één druk op de knop de ruwe meetresultaten uit de GC/MS omzetten naar een rapportage voor de klant.
“Omdat we het analytisch proces zo efficiënt hebben ingericht kunnen we met twee mensen al het werk voor de TOC- en APT-analyses aan. Bovendien is de werkwijze zodanig uitgekristalliseerd dat iemand zonder analytische ervaring na een maandje inwerken al mee kan draaien”, stelt Eli. “Daarbij moet je je er wel altijd bewust van zijn dat het een heel ingewikkeld systeem is. Het werkt allemaal prima, maar alles moet goed gaan om zo nauwkeurig, bijna op de molecuul, te kunnen meten. Zo is er in de buurt van ons pand een fabrikant van dieselmotoren gevestigd die regelmatig tests uitvoert waarbij de uitlaatgassen naar buiten worden geleid en dat zien we terug in de meetresultaten. Weliswaar wordt de lucht die onze cleanroom in komt grondig gefilterd, maar af en toe zie je daar toch iets van terug. Om dat te onderkennen, te kunnen duiden, is het belangrijk dat je niet alleen een goed instrument en dito infrastructuur hebt, maar ook gekwalificeerde medewerkers met kennis van zaken.”
Uitbijters
Hoe zorgvuldig de assemblage van de systemen in de cleanroom ook plaatsvindt, soms komen er toch afwijkingen naar voren. Bij het verlijmen van een koppeling kan bijvoorbeeld de lijm iets te ver zijn doorgelopen, waardoor de gemeten TOC de vereiste maximale grenswaarde overstijgt.
Het is niet altijd even duidelijk wat de oorzaak is van zo’n afwijking. “Zo hadden we onlangs een product met meerdere koppelingen dat herhaaldelijk niet door de test kwam. We hebben toen alle koppelingen apart gesampled en gemeten. Daarbij hebben we ontdekt dat één van die onderdelen restjes machine-olie bevat die langzaam uitgassen en het product vervuilen.”
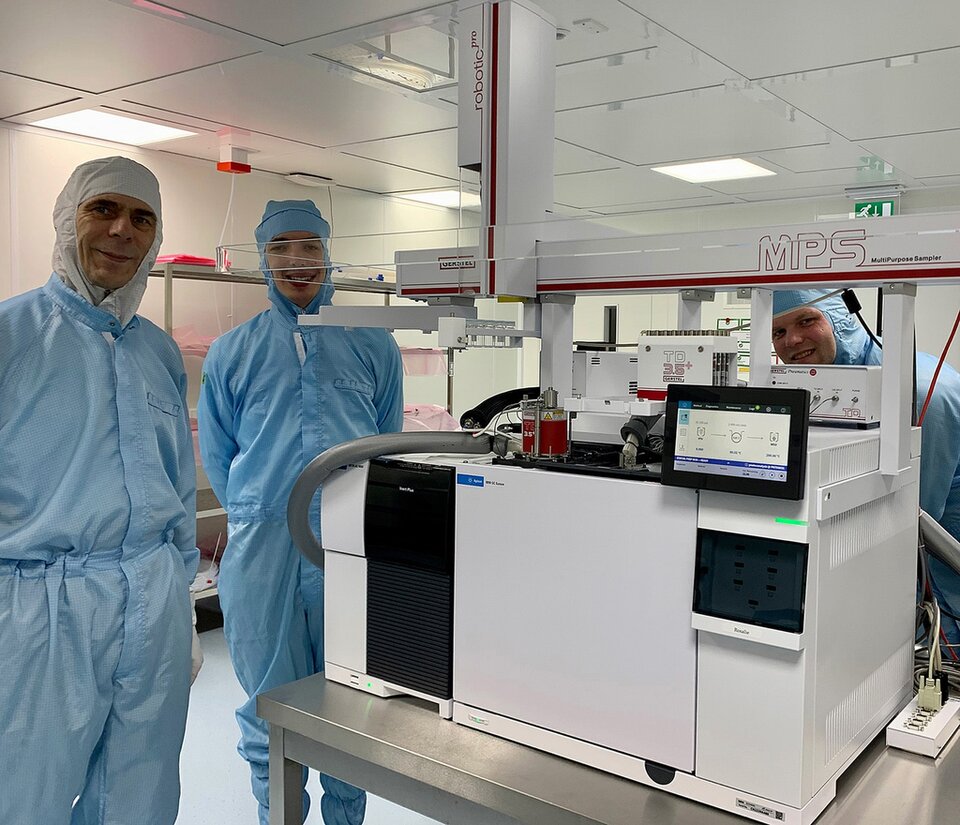
Peter Wijsman, Eli Vanquaille en Richard Bos (v.l.n.r.) bij de door Da Vinci Laboratory Solutions geleverde configuratie voor het bepalen van ppb-hoeveelheden koolwaterstofverbinding. Deze bestaat uit een Agilent GC/MS met thermische desorptie-unit en MPS robotic sampler van GERSTEL.
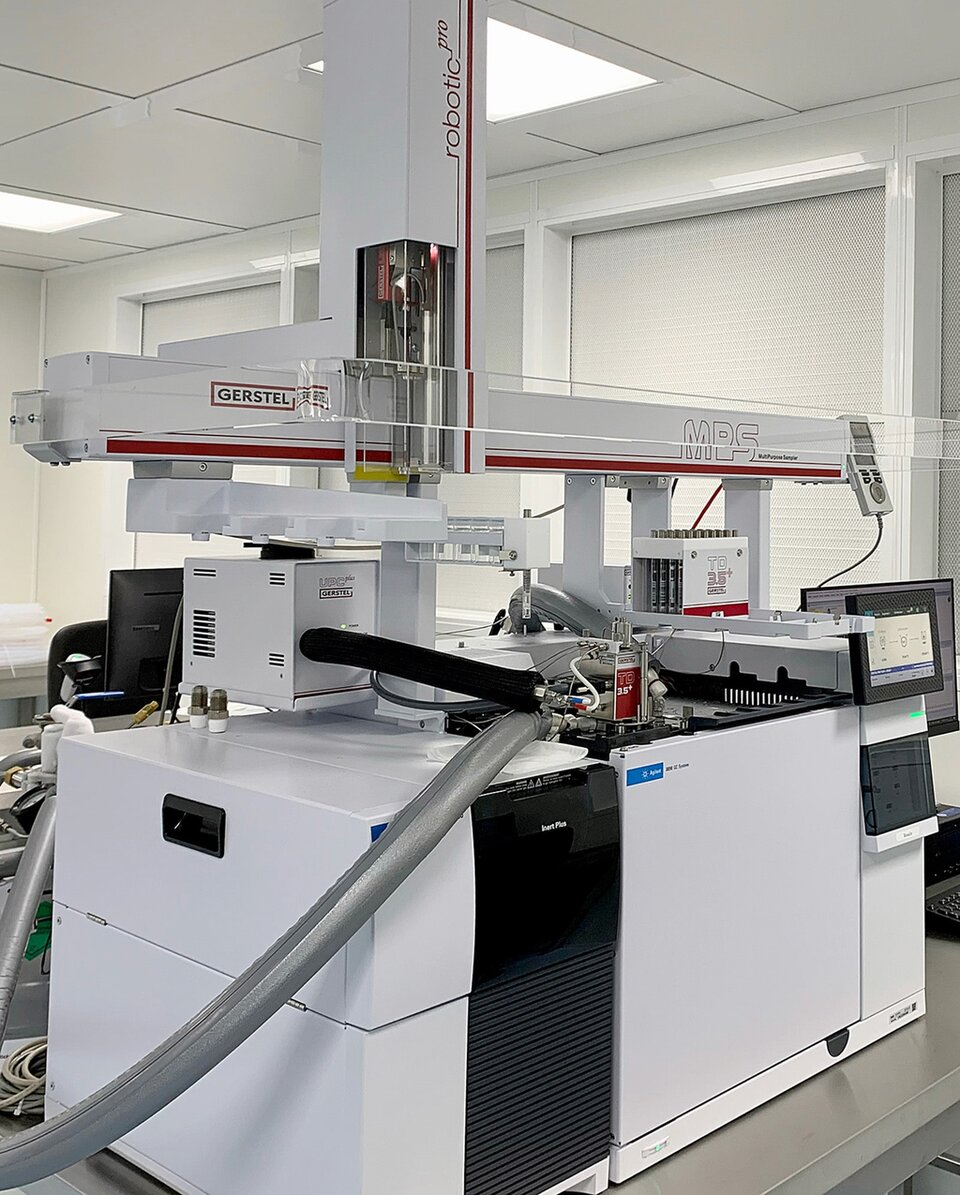
De door Da Vinci Laboratory Solutions geleverde Agilent GC/MS met thermische desorptie-unit en MPS robotic sampler van GERSTEL.
Toegevoegde waarde
De GC/MS wordt ook ingezet bij onderzoek naar nieuwe materialen. “Zo kopen wij bij één van onze leveranciers manifolds in waarop slangen worden aangesloten. Die worden normaliter gefreesd uit plastic, titanium of roestvast staal. 3D-printen maakt het echter mogelijk om interne details te verkrijgen die met conventionele verspaningstechnieken niet gemaakt kunnen worden. Vraag was of het materiaal dat hiervoor wordt gebruikt, geschikt is voor hoge reinheidstoepassingen. Uit metingen bleek dat het materiaal erg veel alcohol uitgast. Dat heeft te maken met de gehanteerde stereolitografie-techniek voor het 3D-printen. Hierbij print je laag per laag een vloeibare foto-actieve hars, die je met UV uithardt. Om nadien de ongeharde hars te verwijderen, wordt het product gespoeld met isopropanol.”
Voor Eli zijn dergelijke onderzoeken de kers op de taart als het aankomt op de dienstverlening naar de klant toe. “Als leverancier streven we ernaar om steeds meer waarde toe te voegen aan de supply chain van de klant. Je voert niet enkel ‘built to print’ werk uit waarbij de klant iets bestelt met die en die specificaties en je het voor ze assembleert, maar je denkt echt mee. Als wij een nieuwe oplossing, een nieuwe kans vinden, bieden we dat aan onze klant aan, zodat die er gebruik van kan maken om een (verdere) voorsprong te krijgen op de concurrentie.”