Veridis geeft met innovatieve analysetechniek boost aan recycling hoogwaardige plastics
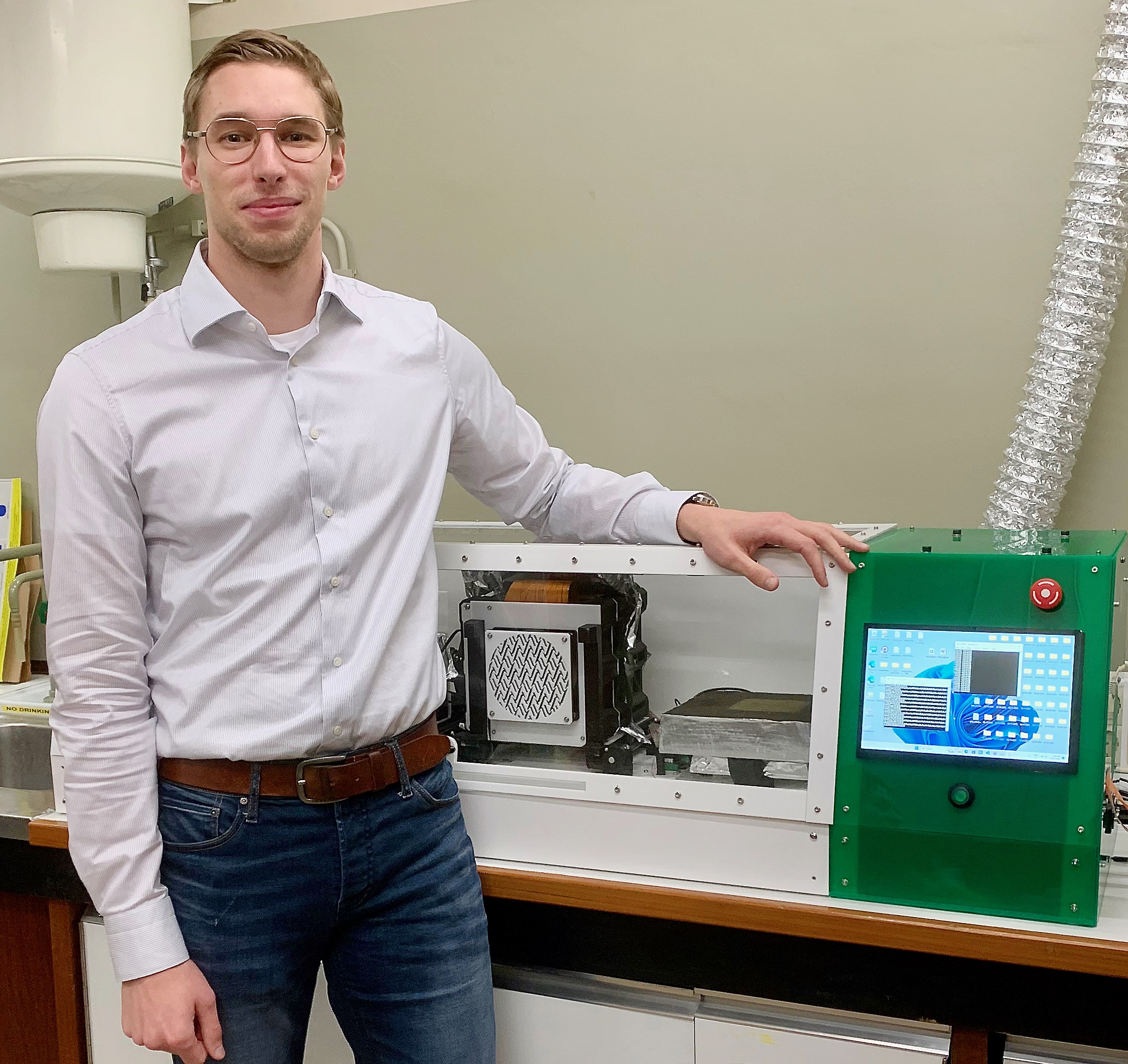
Jeroen Glansdorp, CEO en mede-oprichter van Veridis, bij de MADSCAN T-30 waarmee monsters van 30 gram in één keer kunnen worden geanalyseerd op de plasticsamenstelling.
De Eindhovense startup Veridis heeft een thermische-analysetechniek ontwikkeld, die met een betrouwbaarheid tot 99% de samenstelling van plastics bij recycling processen kan kwalificeren en kwantificeren. De zogeheten MADSCAN onderscheidt zich door het kunnen verwerken van relatief grote, meer representatieve monsters, van nu nog 30 gram tot in de toekomst wel 500 gram. Op basis van de hiermee te realiseren accurate kwaliteitscontrole kunnen door een betere scheiding met gerecyclede plastics meer hoogwaardige producten worden gemaakt. Voor een nog completer analytisch- en procesplaatje kan thermische profiling worden aangevuld met reologische en labextrusietechnieken, waarin Anton Paar voorziet.

De claims ‘100% recyclebaar’ en ‘fles en dop recyclebaar’ zijn misleidend. Dat was in een notendop de uitspraak eind vorig jaar van de Reclame Code Commissie naar aanleiding van een door rechtenstudenten van de Vrije Universiteit ingediende klacht over misleidende claims over de recyclebaarheid van de plastic verpakking van allesreiniger Ajax Limoen door Colgate-Palmolive.
Voor Jeroen Glansdorp, CEO en mede-oprichter van Veridis, komt een dergelijke uitspraak niet echt als een verrassing. “De claim ‘100% recyclebaar’ zegt alleen dat het theoretisch kan. Maar niet dat het gemakkelijk in de praktijk is te realiseren, laat staan dat het daadwerkelijk gebeurt. We zien in de markt veel initiatieven om de recyclebaarheid te verbeteren, maar de materie is heel complex. Niemand kan het in zijn eentje. Overal in de keten moeten verbeterslagen worden gemaakt. Met onze meetoplossing kunnen we op meerdere plekken in de keten, vanaf de sorteerders tot aan de compounders en converters, en zelfs voor het productieproces een bijdrage leveren aan het sluiten van de cirkel.”
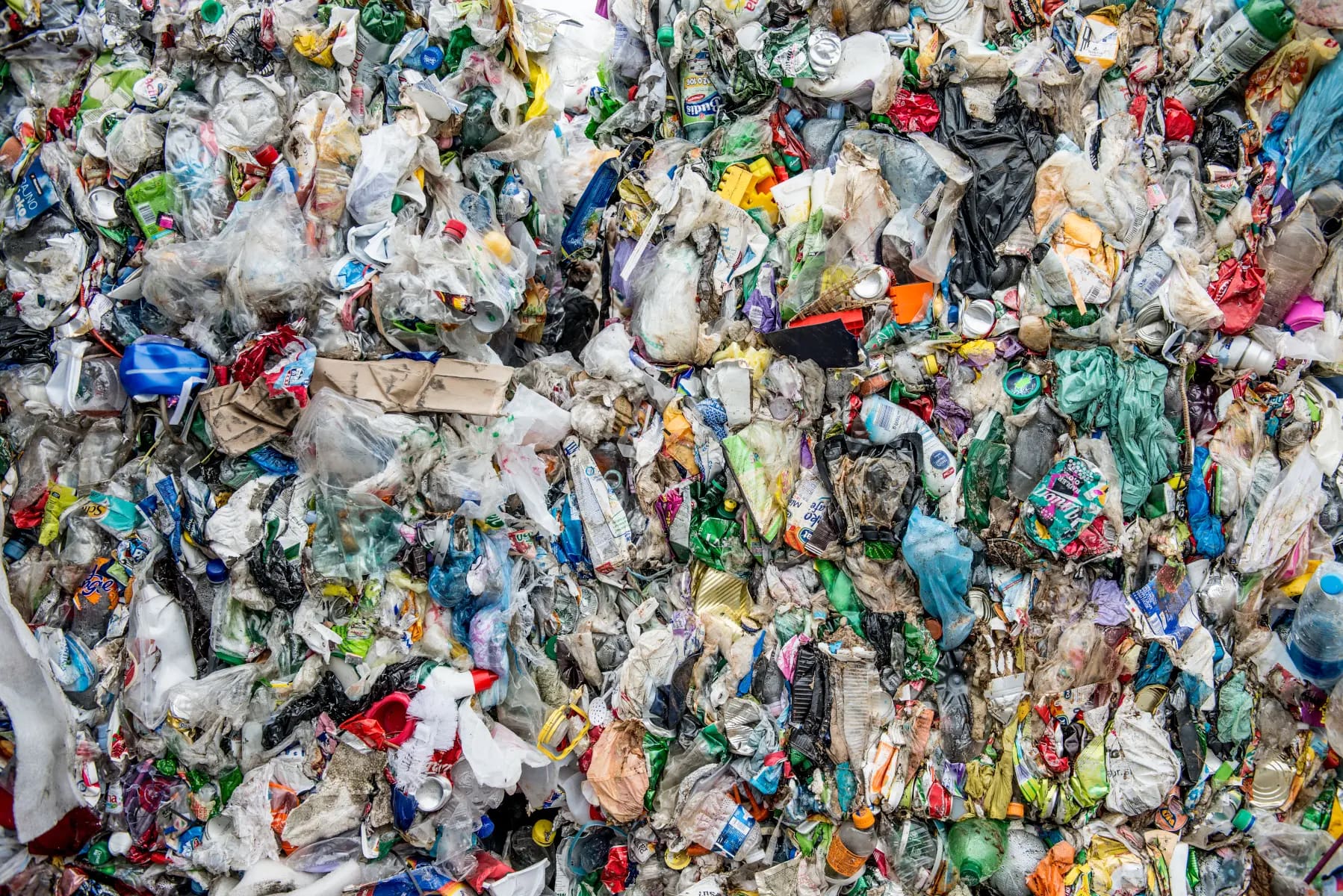
Een ketenbreed probleem bij de recycling van plastics is dat er altijd sprake is van heterogene stromen, met verschillende soorten polymeren.
Heterogene stromen
Een ketenbreed probleem bij de recycling van plastics is dat er altijd sprake is van heterogene stromen, met verschillende soorten polymeren. “De bedrijven die deze stromen verwerken hebben te weinig zicht op de verdeling van die polymeren om daar optimaal mee om te kunnen gaan”, vertelt Marie-José Wolters, die bij Veridis verantwoordelijk is voor sales. “Als je bijvoorbeeld een shampoofles van HDPE wil maken vanuit gerecycled HDPE, dan mag daar hoogstens 3% PP in zitten. Zit er meer in dan breekt het flesje, dat middels een blow moulding proces wordt gemaakt, op de lasnaden. Dat PP-gehalte moet je accuraat in je ingangsmateriaal kunnen meten, zodat je zeker weet dat het aan de specificaties voldoet en je het in productie kan nemen. Of dat je weet dat het niet voldoet en je virgin HDPE kan bijmengen om de ingangsspecifcaties alsnog te halen.”
Aan het vanuit afvalstromen geschikt maken van ingangsmateriaal voor een converter –het bedrijf dat een product maakt van het plastic– gaat een hele serie sorteer-, was- en bewerkingsstappen vooraf, die bij verschillende bedrijven plaatsvinden. Aan het begin van dit proces staan de sorteerbedrijven, die plastic uit afvalstromen selecteren. Daarbij gaat het niet alleen om relatief vervuilde en heterogene post-consumer stromen, zoals PMD. Er zijn ook bedrijven die nauwer gedefinieerde stromen inzamelen. In de regel zijn dat post-industrial en post-industrial end-use stromen. Denk daarbij aan plastic van gebruikt verpakkingsmateriaal. Na het sorteren wordt het in grote balen verpakte plastic bij een ander bedrijf versnipperd tot flakes en gewassen. Deze snippers worden weer ergens anders verwerkt tot een granulaat, dat de converter als grondstof gebruikt voor het maken van nieuwe producten.
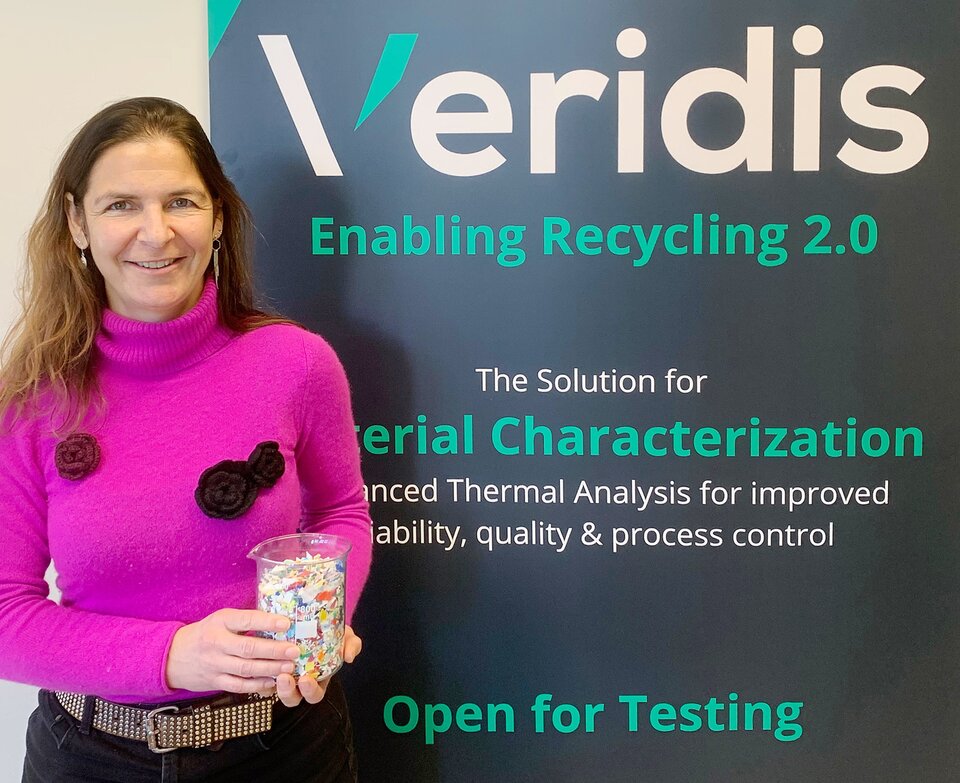
Marie-José Wolters, die bij Veridis verantwoordelijk is voor sales, ziet toepassingen binnen plastic afvalsortering, mechanische recycling, chemische recycling en plastic materiaalverwerking.
Grip op zuiverheid
Elk deelproces in de verwaarding van de gebruikte plastics is erop gericht om tot een zuiverder, minder heterogeen product te komen. Om de effectiviteit van zo’n deelproces te beoordelen, is het zaak om zowel de ingangs- als de uitgangsstroom adequaat te kunnen meten; bij sommige processen zijn ook procesmetingen gewenst. “Het probleem is dat je met de huidige meettechnieken geen goede kwaliteitscontrole kunt uitvoeren. Technieken zijn dermate inaccuraat dat bedrijven te weinig grip hebben op de zuiverheid, zeker in het begin van het recyclingproces”, heeft Jeroen bemerkt. “Kijk bijvoorbeeld naar de verwerking van PMD-afval. Met behulp van NIR wordt een eerste ruwe schifting gemaakt, waarbij het plastic wordt uitgeschoten op productbasis. Ontdaan van metalen en in het oog springende vervuiling kan je dan komen tot een foliebaal, die bijvoorbeeld voor 90% uit PP bestaat, en voor 10% uit andere plastics. Dat kan voor verdere verwerking al een te slechte uitgangspositie zijn om tot bijvoorbeeld 97% zuiverheid voor de compounder te komen. Nu kan je dat NIR-sorteerproces nog wel enigszins tunen, door bijvoorbeeld de sorteerband op een lagere snelheid te laten lopen en minder afval op de band te plaatsen. Echter, omdat je niet adequaat kunt meten, heb je geen trigger om een dergelijke aanpassing bewust door te voeren. En altijd werken met lage snelheden, ook als het niet nodig is, is bedrijfseconomisch gezien niet verstandig. Verderop in de keten speelt hetzelfde. Je kunt de flakes nog een extra wasbeurt geven, of de scheiding op kleur of polymeer nauwgezetter uitvoeren. Totdat je bij de ingangscontrole van de compounder komt. Die kan alleen constateren dat de grondstof niet voldoet en hem terugsturen of, indien mogelijk, bijmengen met virgin materiaal.”
Dit filmpje laat de belangrijkste stappen in de recycling van plastics uit huishoudelijk afval zien. In verschillende stadia van dit proces kan door toepassing van de MADSCAN-technologie het resultaat worden geoptimaliseerd.
Het grote plaatje
Naast kennis over de polymeersamenstelling hebben verwerkers van plastics ook informatie nodig over de reologische eigenschappen van de processtroom. Met aanvullende metingen op dit gebied kan je beter voorspellen hoe processen verlopen. Ook heb je meer handvaten om de benodigde specificaties uit een processtroom te halen.
Anton Paar kan hierin op verschillende manieren bijdragen. Anton Paar heeft analytische methodes zoals FTIR en Raman fingerprint technieken om snel het type plastic te kunnen identificeren, maar ook expertise op het gebied van reologie en extrusie. Met de reometers kunnen de reologische eigenschappen van plastics (zowel grondstof, tussenproduct als eindproduct) worden bepaald en met de Brabender lab-extruders kunnen ook de extrusie-eigenschappen worden gemeten.
Representatief
“Je wilt dus kunnen meten op punten waar je nog wel verbeteringen kunt doorvoeren. Alleen is daar meestal sprake van een grote heterogeniteit aan plastics, waar de huidige meettechnologieën niet goed mee uit de voeten kunnen. Daar hebben we een oplossing voor ontwikkeld, die is gebaseerd op dezelfde fysische principes als bij DSC (differentiële scanning calorimetrie). Deze analysetechniek wordt nu ook al gebruikt voor de analyse van plastics, maar dan onder strak gecontroleerde laboratoriumcondities, voor monsters in de orde van enkele tientallen milligrammen. Met die hele kleine monsterhoeveelheden is het –zeker bij een mix van plastics in een grote partij flakes– bijna onmogelijk om tot een representatief monster te komen, of je moet een ingewikkelde en tijdrovende sampling en monstervoorbewerking toepassen. Iets waar in de recyclingpraktijk geen tijd voor is. Liever wil je zo’n partij op verschillende plekken bemonsteren, de verzamelde flakes bij elkaar stoppen en die in één keer analyseren. Daar zijn we met de MADSCAN een heel eind mee op weg. Inmiddels kunnen we 30 gram monster in één keer analyseren; we streven naar 500 gram”, vertelt Jeroen.
Inmiddels kunnen we 30 gram monster in één keer analyseren; we streven naar 500 gram.
Dealen met gradiënten
DSC is een thermische analysetechniek waarmee gekeken wordt hoe de warmtecapaciteit van een materiaal verandert door temperatuur. Een monster met een bekende massa en een referentiekamer wordt verwarmd of gekoeld met een constante verwarmingssnelheid. De veranderingen in de warmtecapaciteit van het monster worden gevolgd als veranderingen in de warmtestroom in vergelijking met de referentiekamer. De curve met op de Y-as de relatieve verandering in de warmtestroom (W/g) en op de X-as de temperatuur van het monster levert materiaalkarakteristieken als glastransitie-, smelt- en kristallisatietemperatuur op.
“De DSC-laboratoriummonsters zijn niet groter dan een korreltje van enkele milligrammen. Je kunt ze beschouwen als één heat body; je meet ze als één geheel. Als je de monsters opschaalt naar grammen, dan wordt het object veel groter en krijg je tijdens het verwarmen een soort magnetron-effect, waarbij de binnenkant veel minder snel in temperatuur stijgt dan de buitenkant. Je kunt dan niet meer zeggen dat het één object is vanwege de temperatuurgradiënten in je materiaal. Door met sensoren op veel meer plekken te meten kunnen wij op basis van geavanceerde data-analyse tot een gedetailleerd beeld komen van wat er binnenin gebeurt. Dat is niet eenvoudig, en is ook een van de redenen waarom het niet eerder op deze wijze is gelukt –misschien wel geprobeerd– om DSC analytisch op te schalen.”
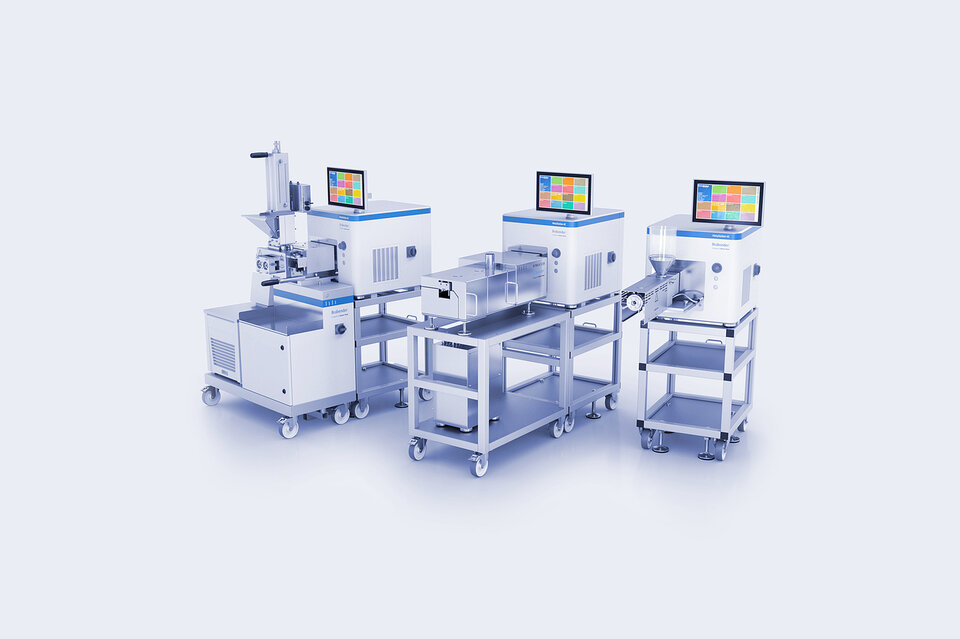
Onder de naam TwinLab zet Anton Paar een hele serie lab- en pilotschaal twin screw extruders in de markt.
Supermodel
In de MADSCAN T-30, het apparaat voor het testen van 30 gram monster, zitten tientallen sensoren, die elk acht keer per seconde een meetwaarde afgeven. Naast de monstertemperatuur wordt ook de heatflow van de warmte-elementen richting het sample gemeten, alsmede het vermogen dat in die elementen wordt gestopt. Omdat je op verschillende plekken in een monster meet, kan je de resultaten ook spatieel differentiëren. Hier ziet meer van materiaal A, daar meer van materiaal B, en dat betekent een bepaalde verhouding voor het totaal. Je kunt zo in een groot monster makkelijker kleine verschillen ontdekken, wat zeker in het geval van de veelal heterogene plasticmonsters van toegevoegde waarde is.
Op basis van zelf ontwikkelde algoritmen, waar veel kennis en expertise in zitten, wordt de rekenintensieve data-analyse gevoed. Daar rollen rapportages uit in de trant van xx% PP en yy% HDPE, waarbij wordt toegewerkt naar een nauwkeurigheid van 1%. Die data-analyse gebeurt op servers van Veridis. “Tijdens de ontwikkeling van het apparaat konden projectpartners monsters naar ons lab sturen, waarop wij de analyse en dataverwerking hebben uitgevoerd. In de nabije toekomst, wanneer die partners het apparaat bij hun productielijnen hebben staan, kunnen ze de data op onze servers uploaden voor analyse, waarna ze in de vorm van bijvoorbeeld een PDF de rapportage ontvangen. Daarmee zal inclusief de analyse circa 1,5-2 uur mee gemoeid zijn”, vertelt Marie-José.
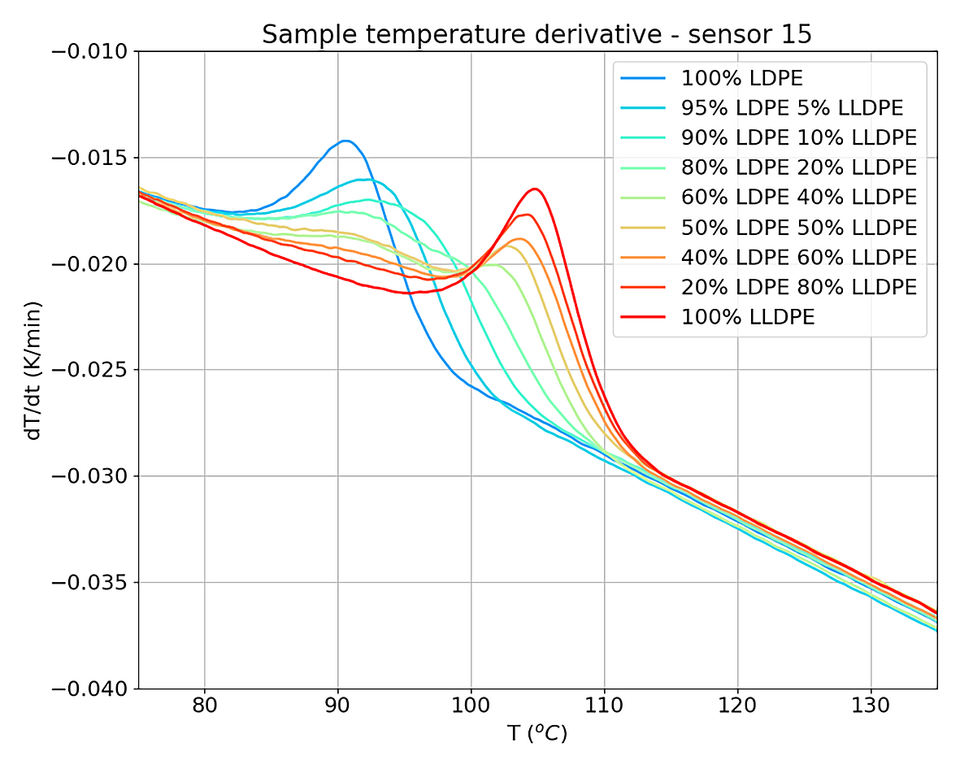
Metingen aan mengsels van binaire virgin polymeer flakes. Door variatie in de afkoelsnelheid kan je aan de hand van de kristallisatiecurves de verschillende LDPE/LLDPE-mengsels duidelijk van elkaar onderscheiden.
Gebruiksvriendelijk
Een ander voordeel van de combinatie van de MADSCAN-technologie en de geavanceerde dataverwerking is dat je rechtstreeks de flakes kunt meten. Dit in tegenstelling tot analytische DSC, waarbij je eerst van de flakes een compound moet maken. Daarbij hoeven de monsters niet vrij van andere verontreinigingen te zijn. Tenslotte kan het apparaat dicht bij de lijn worden geplaatst, en is daarbij door de gebruiksvriendelijkheid ook door niet analytisch geschoold personeel te bedienen, zoals operators, die feitelijk alleen het monster in het apparaat hoeven te plaatsen en op een knop te drukken.
Deze eigenschappen maken dat er veel interesse is in de techniek. In eerste instantie vanuit de sorteerders, maar ook verderop in de keten. “Brand-owners gebruiken de techniek om materiaal te scouten. Ook chemiebedrijven die de eigen regie willen houden door bijvoorbeeld een korrel op de markt te brengen waarin recyclaat zit. Dan moeten ze wel nauwkeurig weten wat ze aan feedstock hebben binnengehaald om aan de specificaties te voldoen”, licht Marie-José toe.
Uiteindelijk hopen we op een punt te komen dat we het aantal dierproeven hiermee kunnen verminderen.
Testen in de praktijk
Veridis werkt inmiddels met verschillende partijen in de keten samen in de (opstart van) projecten om met behulp van de nieuwe techniek klantprocessen te optimaliseren. Zo staat er een project in de steigers met een wasser, die met de extra informatie nu kan meten hoe goed het voorafgaande proces van sorteren op basis van NIR is verlopen, en hoe die het eindresultaat kan optimaliseren. In een andere samenwerking wordt de toegevoegde waarde onderzocht bij het analyseren van de inkomende processtromen en wat het effect is van een procesaanpassing op het eindresultaat.
Jeroen Glansdorp: “In dit najaar is de machine af waarmee pilots bij de recyclers kunnen gaan draaien. Eind volgend jaar willen we de eerste machines uitleveren. Die zullen dan geschikt zijn voor het analyseren van 50 gram. Enkele jaren verder verwachten we de 500-grams-versie te kunnen leveren. Die zal nog veel meer sensoren bevatten, en veel meer rekenwerk vergen!”
Van student tot ondernemer
De kiem voor Veridis is gelegd tijdens een VU Summer School over ondernemerschap. Founder Nigel Visser ging aan de slag met de vraag wat nu echt een probleem is bij de recycling van plastics. Daaruit kwam het ontbreken van een accurate en representatieve kwaliteitscontrole naar voren. Samen met zijn medestudenten Natuurkunde Jeroen Glansdorp en Floris Gerritsen is hij op zoek gegaan naar een technologische oplossing: wat wordt er nu gebruikt, en waarom werkt dat niet; wat zijn alternatieven? “We hebben in die periode, tussen 2018 en 2020, veel gepraat met recyclers en andere partijen uit de plastics industrie. Daarin kregen we de bevestiging dat het een relevant probleem was. Ook raakten wij ervan overtuigd dat we dit technologisch konden oplossen. In juli 2020 hebben we de BV opgericht. Vervolgens hebben we in Eindhoven het HighTechXL venture builder programma doorlopen voor de benodigde bagage qua ondernemerschap”, vertelt Jeroen over de begintijd van het bedrijf.