CDMO Ardena draait in Oss de hand niet om voor de meest complexe API’s
De business-unit API van de Ardena-vestiging op het Pivot Park in Oss produceert in opdracht van klanten uit de farmaceutische industrie actieve farmaceutische ingrediënten (API’s). Chemicus Tom van Daal houdt zich bij de afdeling ontwikkeling bezig met het vinden van geschikte syntheseroutes om dat op een veilige, efficiënte en GMP-compliant manier te kunnen doen. Daarnaast is hij verantwoordelijk voor de flash chromatografie apparaten, die zowel bij ontwikkeling als productie worden gebruikt. Business-unit directeur API-NL, Dirkjan van Zoelen, schetst het grote plaatje en geeft zijn visie op het terughalen van de geneesmiddelenproductie naar Europa.

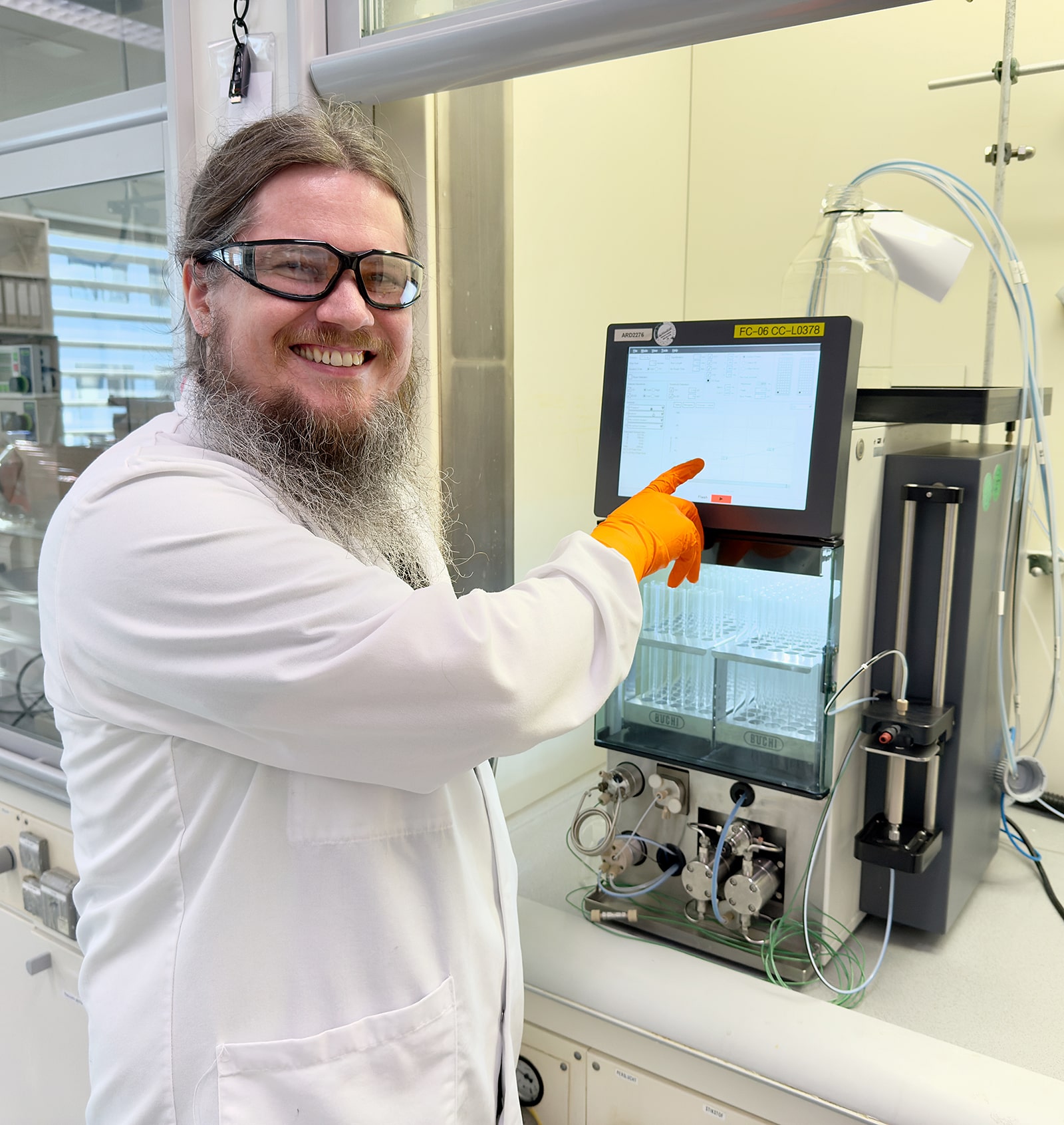
Chemicus Tom van Daal houdt zich bij Ardena Oss bezig met het vinden van geschikte syntheseroutes voor een veilige, efficiënte en GMP-compliant productie. Voor het kolomchromatografisch zuiveren maakt hij gebruik van de BÜCHI C-815 Flash.
In de ruim twee jaar die hij bij Ardena werkt heeft Tom van Daal een grote verscheidenheid aan API’s zien langskomen, van relatief eenvoudige tot hele complexe. “Ze hebben met elkaar gemeen dat het organisch-chemische verbindingen zijn. En dat wij daarvoor een dusdanig proces moeten ontwikkelen dat de betreffende component op een veilige en GMP-compliant wijze kan worden geproduceerd. Dat kan afhankelijk van de fase van klinische ontwikkeling gaan om hoeveelheden tussen pakweg 50 gram en 30 kilogram. De aanvragen beslaan het hele bereik van klinische ontwikkeling, van pre-klinische tox-studies tot aan late klinische fase of commerciële productie.”
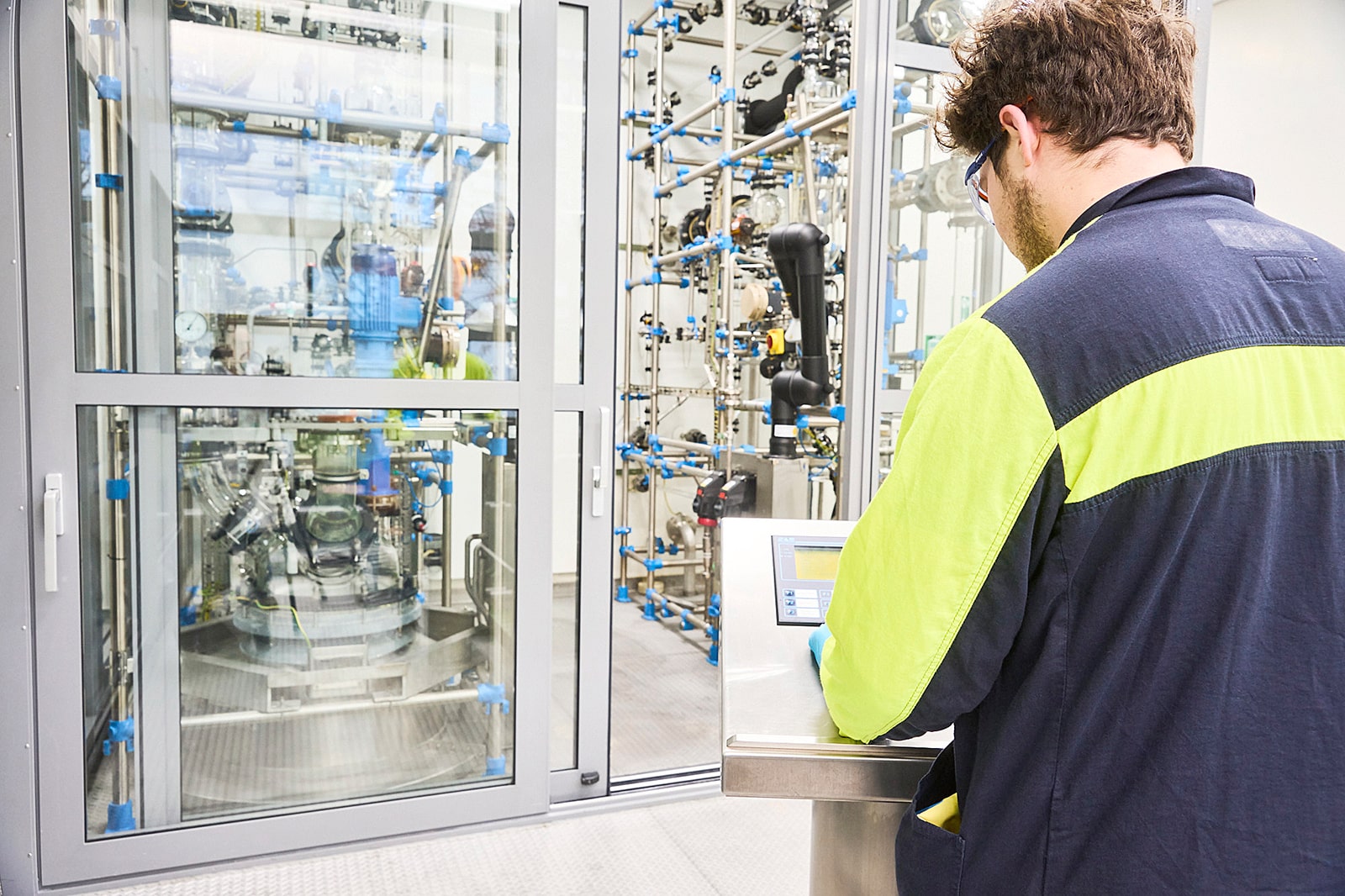
Voor de GMP-productie van API’s zijn er in Oss vijf cubicles, met elk twee reactoren.
Uitdagend
Qua ontwikkeling kan je met diverse uitdagingen te maken hebben. “Soms komt er een opdracht binnen waarvoor je een nieuwe syntheseroute moet uitdokteren. Dan heeft de klant zelf een verbinding gemaakt, die op basis van bepaalde assays als kansrijke kandidaat wordt beschouwd en dus op grotere schaal moet worden geproduceerd. Maar dan blijkt er in hun synthesetraject een zogenaamde ‘substance of very high concern’ (SvHC) te zitten. De EU schrijft voor dat gebruik van deze stoffen zo veel mogelijk vermeden moet worden. Om deze stoffen te omzeilen moet je soms vanaf scratch een heel andere route ontwikkelen. Maar ook als er geen zeer zorgwekkende stoffen in het spel zijn kan het synthesewerk uitdagend zijn. Onlangs kregen we een aanvraag voor een 15- tot 20-staps synthese. Daar zijn we wel even zoet mee!”
Het kan het ook gaan om een stuk procesoptimalisering. “Een klant die met zijn component in het klinische fase 2 traject is beland, wil bijvoorbeeld de hoeveelheid katalysator met 20% verminderen, want dan is er minder GIGO: garbage in, garbage out. Ook wil je soms nog eens kritisch naar de processtappen kijken en met kleine optimalisaties voor net iets minder onzuiverheden zorgen door bijvoorbeeld een reagens minder snel toe te voegen.
Na elke stap zuiveren
GMP stelt eisen tot in de haarvaten van je synthese. Zo is het wenselijk om na elke synthesestap een zuivering, een isolatiemoment in te bouwen. Afhankelijk van wat passend is voor de fase en voor de compound zelf kan dat de ene keer kristallisatie zijn, een andere keer destillatie of kolomchromatografie. “Soms kunnen we daar minder kritisch in zijn, omdat je weet dat je een bepaalde impurity verderop in de synthese gemakkelijk kwijtraakt. Andere keren is zuiverheid echt kritisch, omdat anders een volgende reactiestap niet werkt. Of dat je problemen krijgt met je kristallisatie”, vertelt Tom.
‘Make, analyse & file’: alles onder één virtueel dak
Ardena, met hoofdkantoor in Gent, ontzorgt als CDMO farmaceutische bedrijven voor het traject van het synthetiseren van een API tot aan het filen van een geneesmiddel voor registratie. De dienstverlening is opgeknipt in services als ‘drug substance’ (alles wat nodig is om tot een GMP-geproduceerde API te komen), ‘solid state’ (komen tot de optimale (vaste) productvorm), ‘drug product’ (het GMP-produceren van de API in een geschikte formulering), ‘clinical supply’ (verpakken, labellen), ‘bioanalytical services’ (alle mogelijke analyses op biologisch materiaal welke uit de klinische trials komen) en ‘CMC regulatory services’ (writing & filing). Last but not least is er de business unit Nanomedicines, waarbij het servicepallet is toegesneden op in dit geval nanomedicijnen.
Deze diensten worden verzorgd door een netwerk van inmiddels zes sites, met ieder faciliteiten voor een of meer van die services. De grootste is Ardena Oss, dat op het Pivot Park ruim 75 medewerkers dedicated heeft werken aan ‘drug substance’ en ‘solid state’. Iets verderop is onlangs een nieuwe faciliteit in gebruik genomen voor ‘nanomedicines’, waar zo’n 80 mensen werken. “Met de verhuizing van ‘nanomedicines’ hebben we ruimte gecreëerd voor verdere groei van ‘drug substance’. Bovendien hebben we nu plek voor een hub van ‘bioanalytical services’, dat tot nu toe bij ons zusterbedrijf in Assen was geconcentreerd, maar daar uit zijn jasje groeit. Omdat het vinden van extra personeel in het noorden van Nederland best wel uitdagend is, is besloten om een deel hier onder te brengen. Daarvoor moet wel het nodige worden verbouwd, want alles moet voldoen aan GLP”, vertelt Dirkjan van Zoelen, sinds december 2023 business-unit directeur API-NL.
Eén CDMO
De één-CDMO strategie heeft volgens Dirkjan veel voordelen, zowel voor de klant als voor Ardena. “Als klant heb je maar één CDMO te managen, en niet aparte voor bijvoorbeeld solid state, je API, solid product, regulatory, noem maar op. Daarbij komt dat je bij iedere volgende stap een harde overgang hebt,
van de ene aanbieder naar de andere. Dat vergt veel extra werk qua communicatie, planning en zorgt voor vertraging. Kijk, als wij in Oss de API af hebben, dan kan die naar bijvoorbeeld Gent om te worden geformuleerd. In ons geval kunnen wij die al onder quarantaine shippen, ook al is het CoA nog niet helemaal af, omdat we wel weten dat het goed zit. Als je een harde overgang hebt naar een ander bedrijf, dan ga je die liability niet nemen. Dan moet alles voor 100% zijn dichtgespijkerd.”
“Met meerdere projectteams die met dezelfde klant praten kan je effectief informatie bij elkaar brengen en gerichter voorstellen doen om het proces te versnellen, naar alternatieven te zoeken. We kunnen daarbij flexibel schakelen. ‘Phase appropriate’ werken sluit hier bij aan. Afhankelijk van de fase waarin een medicijn zich bevindt in de ontwikkeling kunnen we iets meer doen, of juist iets minder. Met onze focus op ‘early development’ gaat dat ons ten opzichte van bedrijven die meer op ‘late stage’ en ‘commercial’ manufacturing zitten gemakkelijk af: we weten wat er nodig is, maar vooral wat er niet nodig is.”
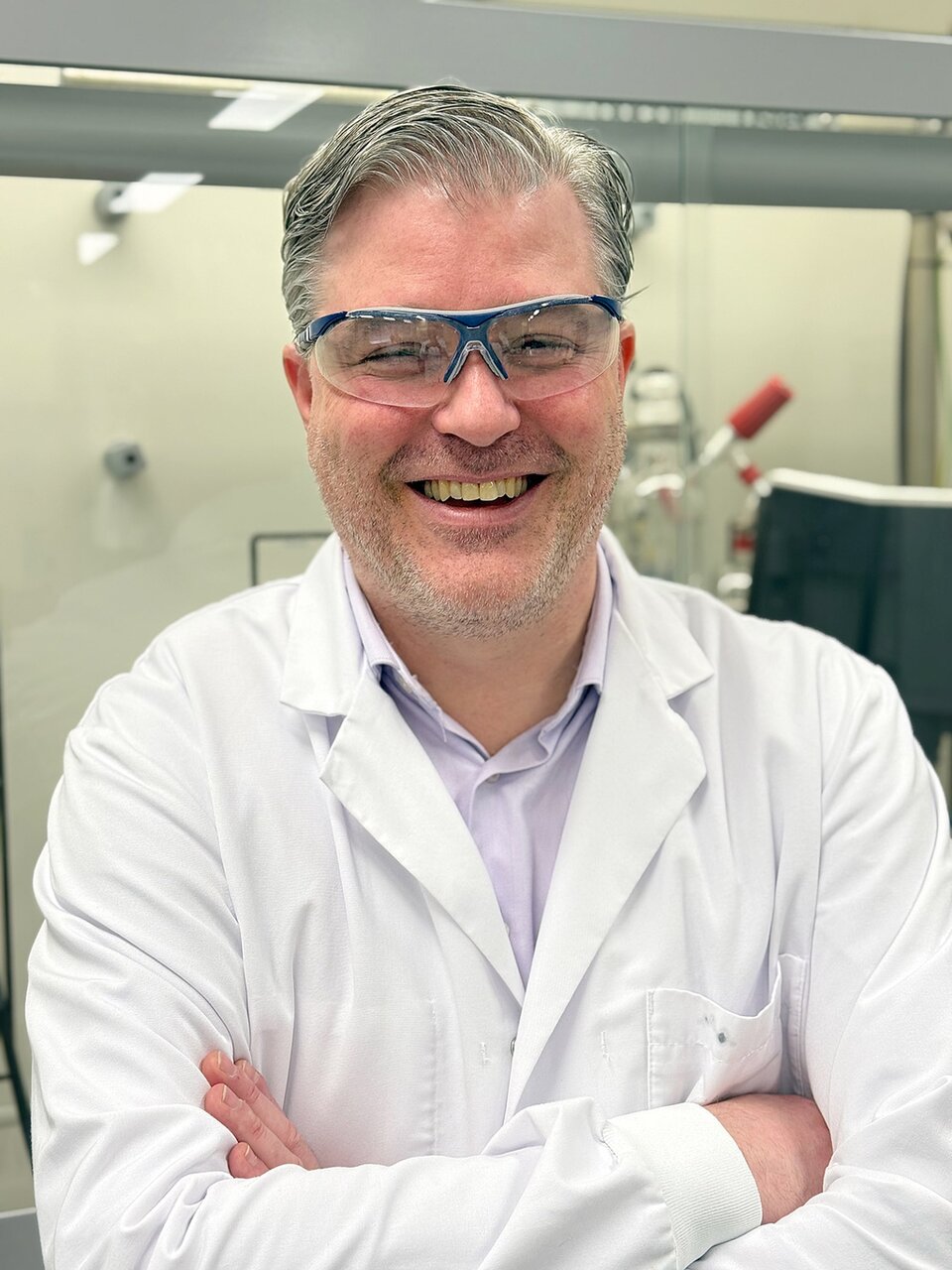
Zo min mogelijk kolomchromatografie?
Vanuit milieu-overwegingen (en ook de daarmee gepaard gaande kosten) staat kolomchromatografie niet bovenaan de keuzelijst als zuiveringstechniek. “Dat heeft ook weer te maken met GMP, die vanwege het risico op cross-contaminatie stelt dat je niets mag hergebruiken qua consumables en materialen. Met een 5-kilo kolom heb je dan sowieso al 5 kilo silica-afval voor op zijn best een halve kilo crude product. Dan gaat er nog aardig wat oplosmiddel doorheen. Dus dat is best wel veel afval voor een klein beetje product. Zet daar tegenover een kristallisatie; daarmee heb je voor een kilo product misschien maar 10 liter oplosmiddel als afval.”
“Maar”, vervolgt Tom, “je kunt niet altijd gaan voor kristallisatie. Dat wil je het liefste wel, maar het gaat gewoon niet altijd. Soms lijken producten zo veel op elkaar dat ze co-kristalliseren. Dan is kolomchromatografie een prima alternatief. Sterker, wij hebben daarin dusdanig veel expertise opgebouwd dat wij middels kolomchromatografie of preparatieve chromatografie ook op grote schaal tot een product kunnen komen dat voldoet aan alle standaarden en eisen die gesteld zijn binnen GMP. Daarin zijn we vrij uniek.”
Wat mij goed bevalt is dat de dode tijd tussen detectie en collectie heel strak is afgeregeld.
Lezen en schrijven met flash
Voor het kolomchromatografisch zuiveren wordt bij ontwikkeling gebruikgemaakt van de BÜCHI C-815 Flash. “In tegenstelling tot de 850, die we dedicated voor productie gebruiken is dit flash-systeem niet geschikt voor preparatieve zuivering. Aanvankelijk hadden we alleen de 850, die een druk van 300 bar aan kan en feitelijk een capture-all systeem is: hij kan uit de voeten met flash-kolommetjes vanaf 4 gram, waar je rond de 50 milligram op kwijt kunt, tot kolommen van wel 5 kilo, waar je in optimale omstandigheden runs van een paar honderd gram per keer kan draaien. Hij is dus geschikt voor zowel het ontwikkel- als het productiewerk. Door de investering in een kleiner gedimensioneerd systeem voor ontwikkeling –de 815 kan drukken aan tot 50 bar– konden we de 850 vrijspelen voor het productiewerk. Afgezien van het feit dat we elkaar niet in de weg lopen, heb je zo ook meer vrijheid voor ontwikkeling. Bij productie vindt alles, dus ook de kolomscheiding, plaats onder het GMP-regime. Bij ontwikkeling hoeven we wat dat betreft minder kritisch naar bijvoorbeeld de gebruikte grondstoffen te kijken”, legt Tom uit, die ook apparatuurverantwoordelijk is voor de flash-systemen.
Vraagbaak
Als apparatuurverantwoordelijke traint Tom nieuwe medewerkers, geeft aan waar je rekening mee moet houden, wat je wel en wat je absoluut niet kan doen. Vanuit zijn ervaring is hij ook de eerste persoon om vragen te beantwoorden. “Tot op zekere hoogte hoor. Het is niet de bedoeling dat je mij voor ieder wissewasje aanschiet, maar vanuit mijn ervaring kan ik vrij gemakkelijk aangeven wat je in een bepaalde situatie het beste kan doen, hoe je een scheiding kan optimaliseren.”
Inmiddels kent hij de systemen van binnen en buiten, zeker de 815 waar hij het meeste mee werkt. “Wat mij goed bevalt is dat de dode tijd tussen detectie en collectie heel strak is afgeregeld. Daardoor mis je eigenlijk niets van je compound, wat voor ons heel belangrijk is. Als je een goede TLC neemt kan je dat gewoon één op één transleren naar kolomchromatografie. Dat is wel iets wat andere systemen minder goed doen. Hij geeft echt controle over je hele zuivering.”
Wèl in mijn backyard, met flowchemie
Dirkjan van Zoelen is net als velen niet blij met de Europese afhankelijkheid van China en India wat betreft de ontwikkeling en commerciële productie van geneesmiddelen. “Dertig, veertig jaren geleden hebben we het best wel gevaarlijke en milieu-onvriendelijke productiewerk afgestoten en daarvoor goedkopere geneesmiddelen teruggekregen. We zijn daarin doorgeschoten, en hebben de controle verloren. Om die weer terug te krijgen is het niet haalbaar om dan in Europa maar weer allerlei ‘old style’ fabrieken uit de grond te stampen. Want te duur, te vervuilend, te gevaarlijk.”
De oplossing ziet hij in innovatie. “Door innovatie kunnen we vele malen efficiënter en goedkoper produceren. Op de eerste plaats door –oneerbiedig gezegd– de mens eruit te halen. Niet alleen door automatisering en robotisering, maar ook door veel slimmer met hulp van AI ‘design of experiments’ en syntheseroutes uit te denken en te realiseren.”
Continuous manufacturing
Voor het terughalen van productie moeten we volgens Dirkjan gaan inzetten op continuous manufacturing, via flowchemie. “Een nitrering op 10.000 liter schaal; zwavelzuur met salpeterzuur en dan in situ HONO vormen om te nitreren op 10.000 liter schaal. Dat gaat gewoon niet meer. In continusystemen kan dat wel. Die hebben bovendien als voordeel dat ze veel energie-efficiënter en veiliger zijn.”
Ardena is zelf ook al actief op het gebied van flowchemie. Zo participeert het binnen het Sprong consortium, in het CONNECT-project (‘Collective process development for an innovative chemical industry’), waarin bedrijven en kennisinstellingen samenwerken in het komen tot industriële toepassing van continuous manufacturing. “Belangrijk zijn de field labs in Utrecht, Rotterdam en Maastricht, waar je laagdrempelig, ondersteund door specialisten, verschillende technieken kunt uitproberen. Inmiddels zijn we bij Ardena al een stapje verder. Een samenwerking met producent van continuous flow apparatuur Ou Shisheng (Beijing) Technology en ChemSPX is recentelijk uitgemond in de installatie van het MO-FLOW-S platform. Hiermee kunnen we expertise opbouwen in proces-R&D en kleine-schaal productie aan de hand van microtubulaire technologie voor onder meer fotochemische processen.”
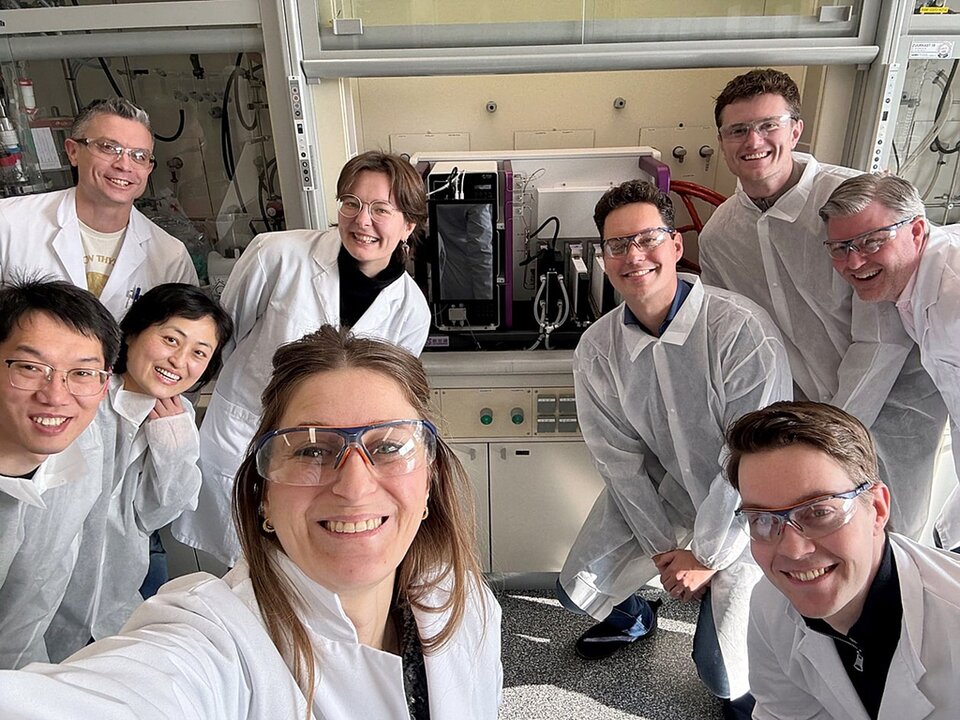
Voor het terughalen van productie moeten we gaan inzetten op continuous manufacturing, via flowchemie.
Minder werk
Tom heeft weinig onderhoud aan het systeem. “Voorwaarde is wel dat je hem aan einde van de rit goed schoonmaakt. De handleiding is daar duidelijk in. We hebben onze procedures daar netjes op aangepast. Dan gaat er eigenlijk nooit iets mis. Inclusief schoonmaken ben je sowieso maximaal twee uur kwijt met een scheiding waarvoor je met een handmatige kolom rustig tenminste een halve dag moest uittrekken. Wat dat betreft is het een enorme life and time saver!”