TPRC intensiveert onderzoek naar de recycling van vezelversterkte thermoplasten
Een in belang groeiend aandachtsgebied in de research roadmap van het ThermoPlastic composite Research Center (TPRC) in Enschede is alles wat te maken heeft met duurzaamheid van vezelversterkte thermoplasten. Daarbij gaat het met name om onderzoek op het gebied van recycling van deze lichtgewicht materialen. Gelden vanuit het Nationale Groeifonds voor hieraan gelieerde projecten zijn onder andere besteed aan een extruder, waarmee op labschaal onderzoek naar recyclingprocessen kan worden uitgevoerd.

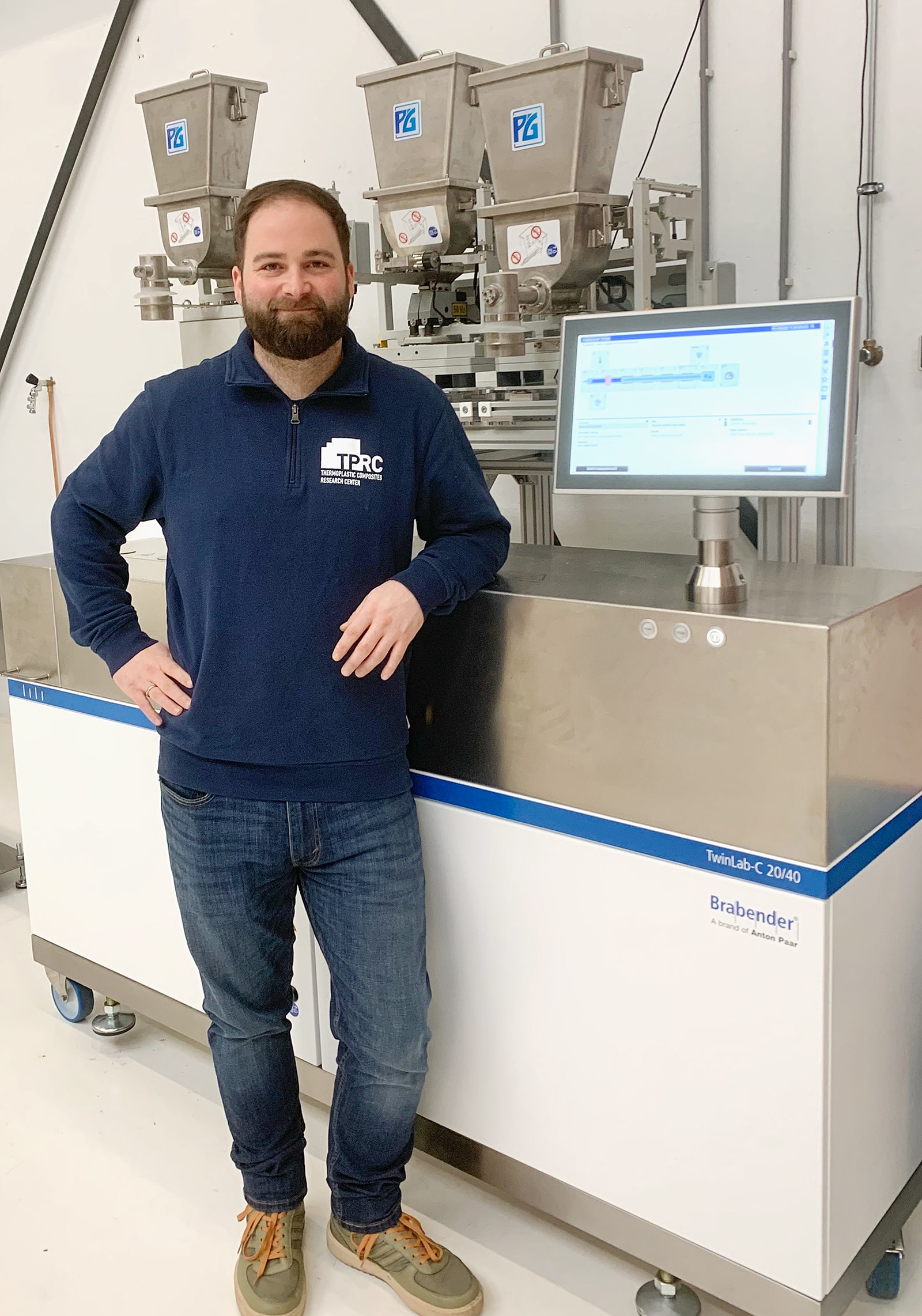
Engineering Manager Lazlo Giesgen bij de door Anton Paar geleverde TwinLab-C 20/40 extruder van Brabender, die vorig is aangeschaft in het kader van onderzoek naar de recycling van vezelversterkte thermoplasten.
“Vezelversterkte thermoplastische materialen hebben ideale eigenschappen voor recycling, zeker in vergelijking met thermoharders”. Geen onverwachte uitspraak van iemand die werkt bij het TPRC, dat als missie heeft ‘het stimuleren van het gebruik van thermoplastische materialen’. Maar ook objectief gezien valt er geen speld tussen de argumentatie van Lazlo Giesgen, Engineering Manager bij de Enschedese non-profit onderzoeksorganisatie, te krijgen. “Met thermoharders heb je wat betreft recycling weinig speelruimte. De door verhitting uitgeharde materialen zijn vast in een vernette structuur en je kunt ze niet meer in een later stadium smelten om ze opnieuw toe te kunnen passen. De thermoplastische matrix kan je daarentegen op ieder moment weer smelten, waardoor je het materiaal bijvoorbeeld in een nieuwe vorm kan persen. Je kunt de vezels eruit halen, zodat je vezels en matrix apart kunt recyclen. Maar je kunt ook gewoon het volledige composietmateriaal (thermoplast en vezel) hergebruiken door het bijvoorbeeld te versnipperen en de snippers als grondstof voor een ander proces te gebruiken.”
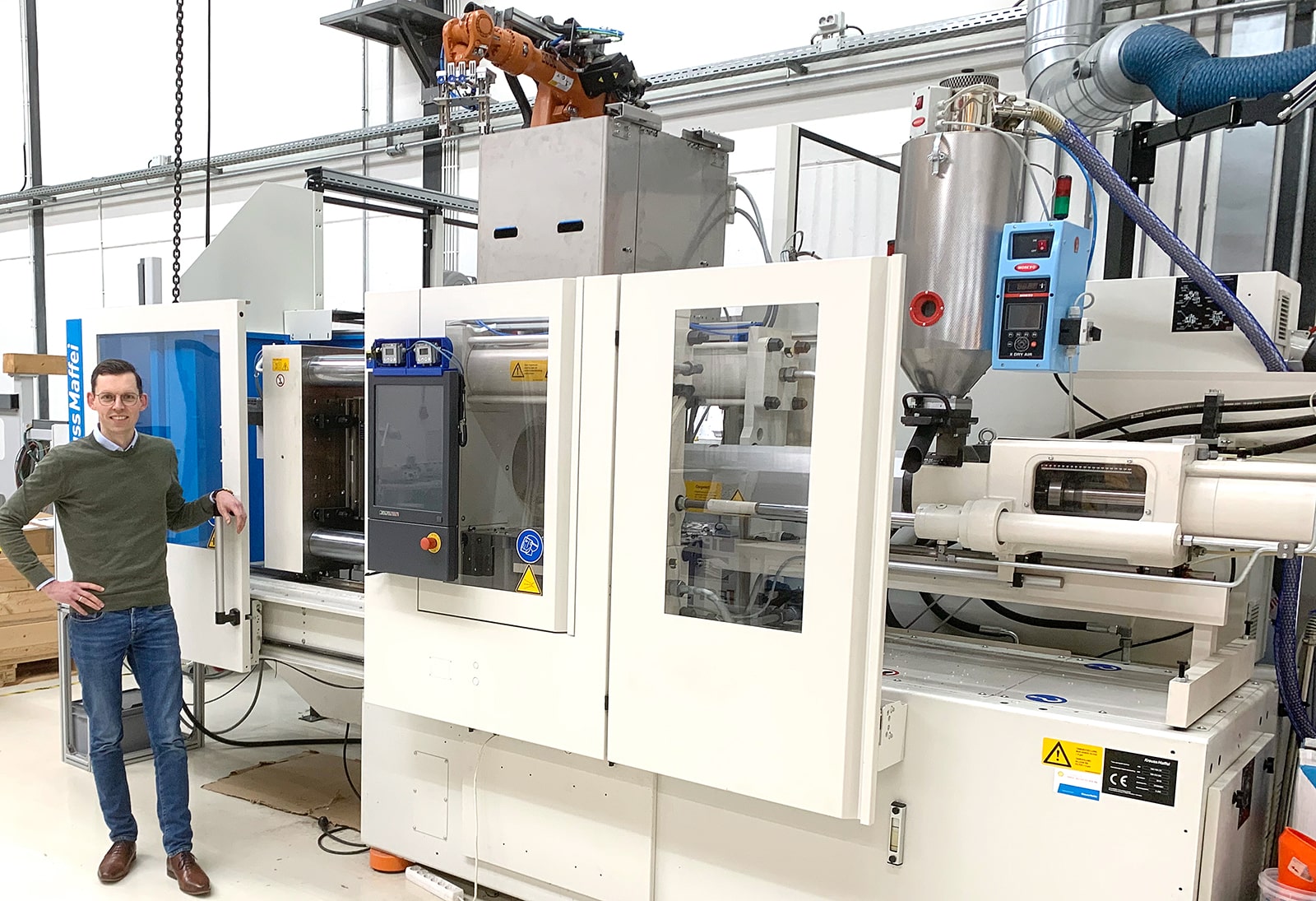
Business developer Rens Pierik bij een combinatie van een pers en een spuitgietmachine, waarbij nieuw en gerecycled materiaal samen kunnen worden toegepast.
Ontwerpen voor recycling
Net als bij de andere onderzoekspijlers van TPRC draait het bij het recyclingonderzoek om de interactie tussen materiaal en proces. Hoe moet je omgaan met het materiaal om het beste eruit te halen tijdens recycling. Hoe moet je het recyclen; wat gebeurt er met het materiaal tijdens recycling; wat zijn de eigenschappen na recycling? “Om daar in generieke termen een antwoord op te geven, moet je dealen met tal van proces- en materiaalparameters, die veelal de complexiteit van de puzzel nog verder vergroten. Neem bijvoorbeeld de vezelarchitectuur. Een vrij nieuwe trend is om unidirectioneel versterkte materialen te gebruiken. Dat betekent dat je binnen één laag alle vezels in één richting hebt. Dit als tegenhanger van geweven structuren, waarbij vezels loodrecht op elkaar zijn georiënteerd. Dan kan je verschillende lagen, met verschillende oriëntaties op elkaar stapelen, zodat je sterkte en stijfheid in verschillende richtingen hebt. De platte vorm wordt niet zelden omgezet in een 3D-geometrie, al dan niet met plaatsspecifieke diktevariaties. Je kunt je voorstellen dat bepaalde structuren gemakkelijker uit gerecycled materiaal te maken zijn dan andere”, licht business developer Rens Pierik toe.
TPRC in het hart van het ecosysteem rond thermoplastische composieten
Met inmiddels een kleine 50 medewerkers, merendeels onderzoekers, waaronder 10 tot 15 promovendi, vervult TPRC al meer dan 15 jaar een voortrekkersrol in onderzoek aan vezelversterkte thermoplasten. Gestart met Boeing, Toray (voorheen Ten Cate), GKN Fokker en TU Twente heeft het TPRC vandaag de dag 22 partners vanuit alle geledingen van de waardeketen, van materiaalleveranciers tot machine- en apparatenbouwers, van kennisinstellingen tot OEM’s. Er zijn tier 1 en tier 2 partners. Tier 1 partners betalen meer contributie dan tier 2 partners en krijgen daarvoor meer invloed op de research roadmap, het pre-competitieve meer generieke en fundamentele onderzoek op het gebied van de interactie tussen materiaal en proces, dat de kern vormt van de research bij bij TPRC. De resultaten van dat onderzoek zijn voor beide groepen van partners beschikbaar. Daarnaast vindt vertrouwelijk onderzoek plaats in bilaterale projecten, dat door de betreffende partner wordt gefinancierd. Een dergelijk project kan worden opgestart naar aanleiding van resultaten uit het roadmap onderzoek, die de partner in zijn eigen meer praktijkgericht onderzoek wil inpassen. TPRC kan dan helpen met bijvoorbeeld materiaalkarakterisatie of andere soorten testen.
Het onderzoeksbudget wordt voor circa 90% besteed aan het roadmaponderzoek; de rest gaat op aan het bilaterale werk en cursussen om professionals in het veld op te leiden. Ongeveer de helft van de inkomsten komt uit de vergoedingen van de tier 1 en tier 2 partners. Financiering vanuit het Nationale Groeifonds, die twee jaar geleden van start is gegaan, staat voor 40% van de inkomsten. De rest komt uit het bilaterale werk en de cursussen. Met de impuls vanuit het Nationale Groeifonds heeft TPRC de onderzoekscapaciteit bijna kunnen verdubbelen.
Gedrag tijdens recycling
In het kader van het IMMORTAL-project, een acroniem voor ‘Investigating Materials and Methods for Optimal Recycling of Thermoplastic composites in Aircraft Life cycles’, probeert TPRC onder andere meer grip te krijgen op de mechanismen achter het extrusieproces, de recyclingstap na het mechanisch kleiner maken (shredderen) van het te recyclen materiaal. “We richten ons hierbij op het karakteriseren en beschrijven van de kwaliteit van het materiaal als functie van de procesparameters en de ontwikkeling van methoden voor materiaalkarakterisering voor processimulatie. We willen bijvoorbeeld de invloed van verontreinigingen, vezellengte, mengkwaliteit en procesgeschiedenis zodanig in kaart brengen dat we die kunnen vertalen naar materiaalkaarten en richtlijnen voor verwerking en ontwerp”, beschrijft Rens de doelstellingen van het project, dat een combinatie is van twee grote door de overheid gefinancierde projecten: NXTGEN en FENIKS, die zijn gericht op het maken van lichtgewicht materialen voor e-mobility respectievelijk de luchtvaartsector.
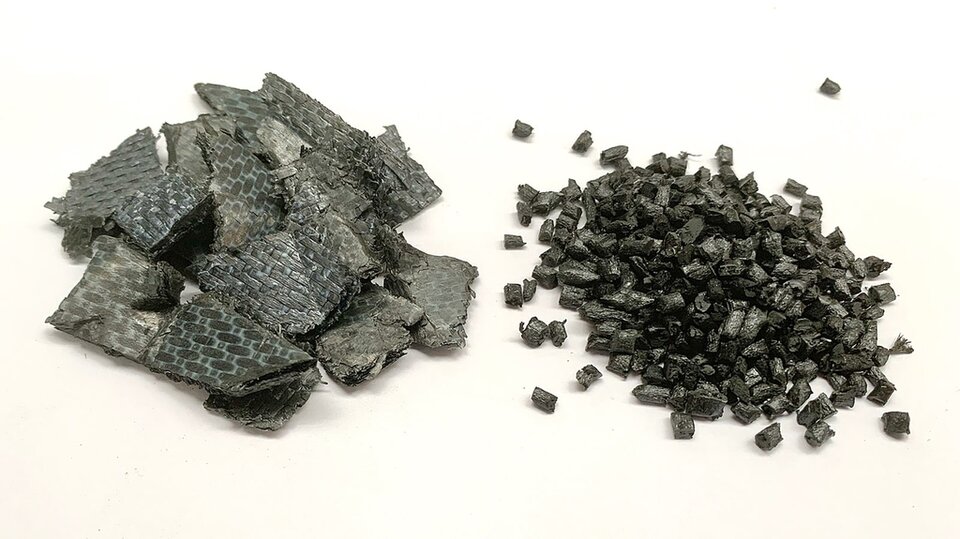
Gerecycled thermoplastisch materiaal voor en na de procesgang in de extruder. De pellets kunnen worden gebruikt in de spuitgietmachine.
Extruder
In een extruder, die via feeders wordt gevoed met een stroom van tot kleinere stukjes gemaakt composietmateriaal, vindt onder verhoogde temperatuur een mechanisch mengproces plaats. Hierbij wordt het te recyclen materiaal in een dubbele-schroef extruder gebracht, die onder hoge kracht het materiaal verder verkleint en geschikt maakt om verder te worden verwerkt in reguliere productieprocessen als spuitgieten en persen.
Deze extruder, een TwinLab-C 20/40 van Brabender, een merk van Anton Paar, is speciaal voor het recycle-onderzoek aangeschaft en is sinds eind 2024 operationeel. Lazlo heeft voor zijn zoektocht naar de meest geschikte extruder vijftien verschillende fabrikanten onder de loep genomen. Uit een shortlist van vijf is de TwinLab gekozen. “Deze extruder met dubbele schroef heeft voor ons de perfecte maatvoering; niet te groot en niet te klein. Bedenk dat de materialen waar we mee werken relatief duur zijn, tot wel 150 euro per kilo. Met deze machine op labschaal kunnen we kleine batches verwerken, wat ook voor onze partners een aantrekkelijke optie is. Verder zijn de schroefdraden voorzien van een speciale, zeer slijtvaste coating, die bestand is tegen de beruchte abrasieve werking van de koolstofvezels. Wat ook opvalt is dat het extrudergedeelte vol zit met druk- en temperatuursensoren zodat we heel gedetailleerd het extrusieproces kunnen regelen en monitoren. Dat is voor gerecyclede materialen essentieel: door structurele veranderingen is de dichtheid niet constant, en die moet je voor een juiste interpretatie van de testgegevens haarfijn kunnen monitoren.”
Bedenk dat de materialen waar we mee werken relatief duur zijn, tot wel 150 euro per kilo.
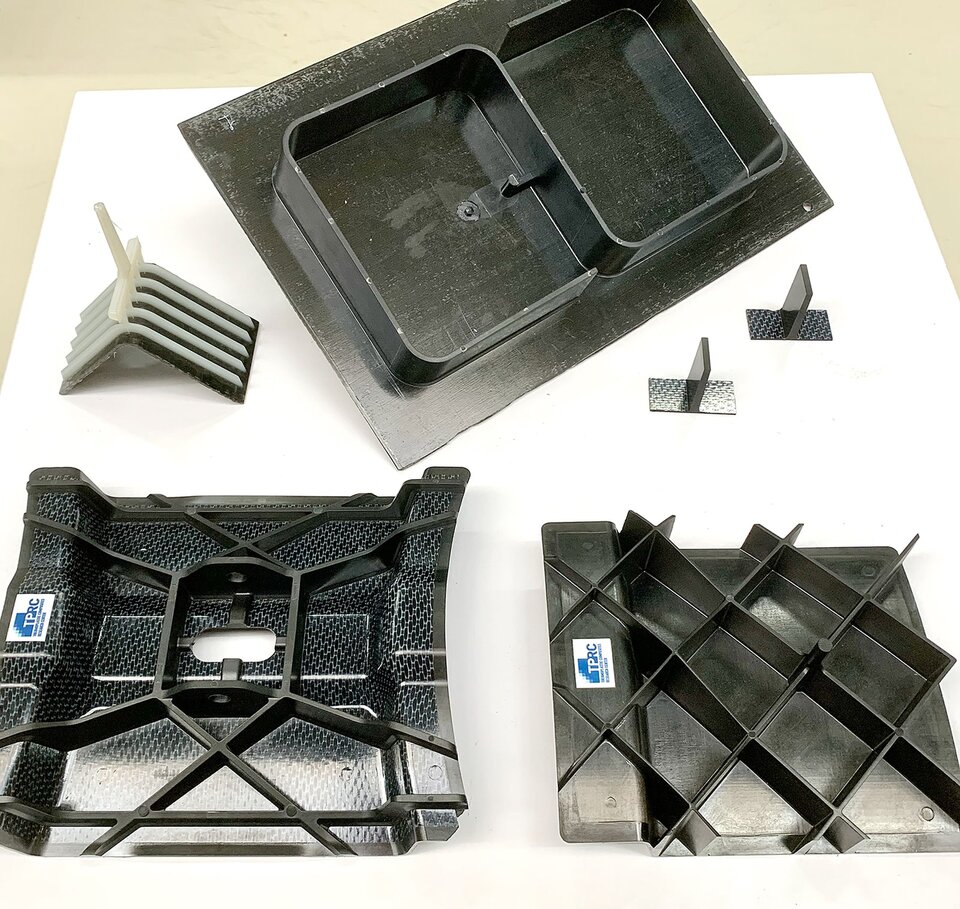
Voorbeelden van complexe constructies, die zijn gemaakt op de gecombineerde pers en spuitgietmachine.
Schelp
Een heel praktische eigenschap, die Lazlo niet eerder bij andere extruders had gezien, is de zogenaamde ‘clamp shell’ cilinder, die zich laat openen als een schelp. “Je kunt door deze constructie in een keer de hele cilinder open maken, waarbij je zicht hebt op de twee schroefdraden en het proces. Dat geef de mogelijkheid om direct monsters te nemen, bijvoorbeeld voor meting van de vezellengte of de kwaliteit van het mengen. Dit kan in verschillende stadia van het mengproces. Aan het begin en het aan einde van de schroeven, en alles daar tussenin. Zo kan je goed in kaart brengen wat er gebeurt met het materiaal tijdens het mengproces. Bovendien is het reinigen heel efficiënt. Je hoeft hem namelijk niet door te spoelen. Je laat hem afkoelen, opent hem, neemt je monsters, maakt de rest schoon, sluit hem weer en klaar is kees”, aldus Lazlo, die verder ook zeer te spreken is over de technische ondersteuning, het gegevensbeheer en de bediening op afstand.
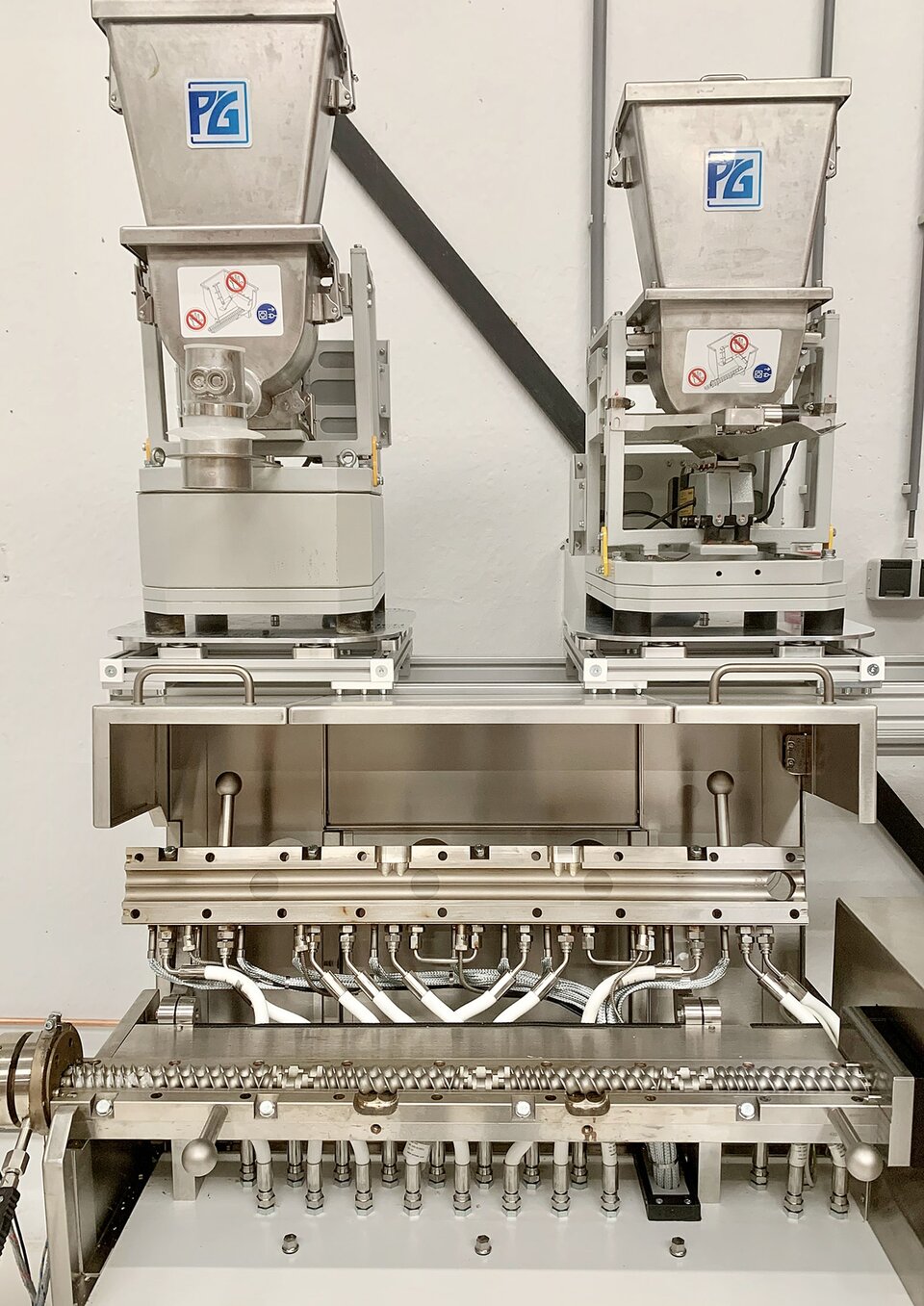
De ‘clamp shell’ cilinder, die zich laat openen als een schelp, geef de mogelijkheid om direct monsters te nemen, bijvoorbeeld voor meting van de vezellengte of de kwaliteit van het mengen.
Flexibel
Met een zestal openingen om materiaal toe te voegen is het extrudersysteem zeer adaptief, wat voor R&D-werk een uitkomst is. Zo zijn er twee openingen aan de zijkant waardoor je extra materiaal (zoals losse vezels) geforceerd, dus met kracht, kan toevoegen. Een viertal openingen aan de bovenkant biedt flexibiliteit om bijvoorbeeld eerst een polymeer en later vezels te doseren, zodat je kan spelen met de procestijd wat weer impact heeft op de mate van vezelbreuk, vezellengte en de uiteindelijke mechanische prestaties. Ook kunnen verontreinigingen worden toegevoegd, die je er in de praktijk zomaar bij te recyclen materiaal bij kan krijgen, zoals verpakkingsfolie en verf.
Massa kweken en samenwerken
Om recycling van thermoplasten tot een succes te maken moet er nog wel een afvalstroom op gang komen. Ten opzichte van andere materiaalgroepen, recycle-kampioenen als plastics en metalen, valt de productie van thermoplastische materialen in het niet. En van al dat in de afgelopen twintig jaar geproduceerde materiaal is er heel wat dat nog niet aan zijn end-of-life toe is. Bijvoorbeeld uit vliegtuigen die gemakkelijk een jaar of dertig meegaan. De grote Boeings en Airbus toestellen bestaan weliswaar voor de helft uit composieten, maar dat zijn vooral thermoharders; slechts een paar procent is thermoplast.
Een uitdaging zit hem ook in de identificatie van de verschillende soorten thermoplasten en vezels in één partij. “Een scheidingssysteem, zoals bij plastics op basis van NIR, gaat hier niet werken. Voor de thermoplasten kan een breed scala aan polymeren worden gebruikt. Deze zijn heel lastig te identificeren, zeker als er koolstofvezels –de nummer één voor hoogwaardige lucht- en ruimtevaarttoepassingen– in het spel zijn. NIR is dan sowieso geen optie vanwege het hoge koolstofgehalte in het materiaal”, aldus Rens.
Naast gemengde afvalstromen kan je voor recycling ook zuivere, homogene afvalstromen gebruiken. “Dat is bijvoorbeeld het afvalmateriaal dat je bij productie overhoudt. Je weet precies welk materiaal je erin hebt gestopt, dus je weet ook wat eruit komt. Door dat restmateriaal netjes per soort thermoplast te bewaren heb je op den duur de beschikking over homogene partijen die efficiënter kunnen worden gerecycled. Scheiden bij de bron als het ware, dat je ook kunt doortrekken naar stromen van gebruikt materiaal. Door nauwgezet te documenteren in welke producten welke thermoplasten zijn gebruikt kan de afvalverwerker te zijner tijd een database raadplegen om te achterhalen met welke thermoplasten hij te maken heeft. Een dergelijk systeem vergt wel samenwerking tussen alle stakeholders in de hele keten, van materiaalproducenten en productiebedrijven tot fabrikanten van eindproducten en eindgebruikers”, aldus Rens. “Voor nu is het wel zo pragmatisch om je te richten op de afvalstromen binnen productie. Dan weet je precies om welke materialen het gaat en dat ze nog schoon zijn.”
Richtlijnen
De onderzoeksmogelijkheden zijn legio. Lazlo: “Je kunt bijvoorbeeld uitzoeken hoe vaak je een vezelversterkte thermoplast kunt recyclen. Is dat vijf keer, tien keer, vijftien keer? Niemand die daar nog het fijne van weet. Het is wel zo dat iedere thermische behandeling een zekere mate van degradatie met zich meebrengt. Maar op welk punt is de degradatie zo hoog dat je het materiaal echt niet meer kunt gebruiken? En in het verlengde daarvan: hoe kunnen we het beste nieuw en gercycled materiaal combineren, zodat het later ook weer te recyclen is? Hoe ontwerp je met gerecyclede materialen om bepaalde eigenschappen te bereiken?”
Een en ander moet leiden tot fundamentele richtlijnen rond proces- en materiaalparameters, die zo ver als mogelijk onafhankelijk van de gebruikte apparatuur zijn. “Het kunstje dat wij met de Brabender en onze productiemachines doen, moet door anderen binnen en buiten ons partnernetwerk kunnen worden gereproduceerd in hun eigen machinepark, op de door hen gewenste schaalgrootte. Als dat lukt zijn we weer een stapje verder in onze missie: het stimuleren van het gebruik van thermoplastische materialen voor lichtgewicht vervoer.”